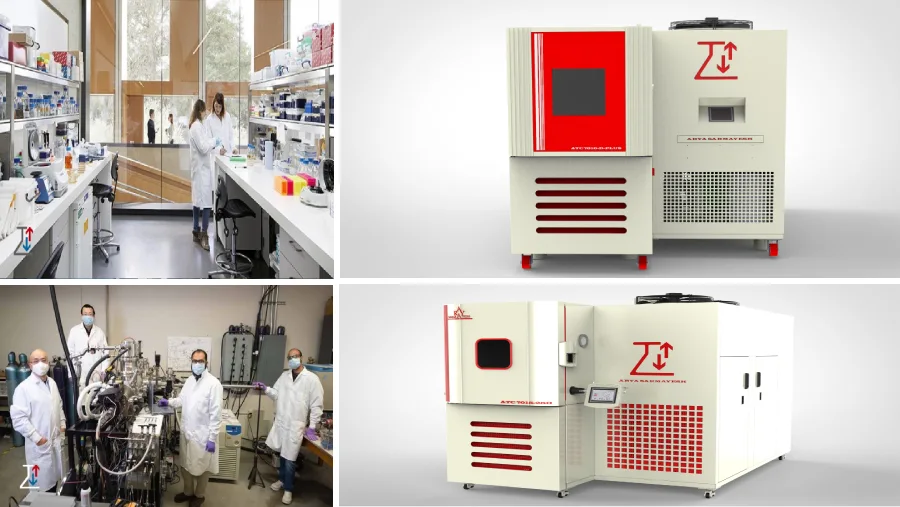
Thermal shock testing is a critical process in materials science, engineering, and quality control that evaluates how a material or component reacts to rapid temperature changes. This test simulates the stresses and potential failures that occur in real-world environments where materials are exposed to extreme or fluctuating temperatures. Thermal shock testing is essential for ensuring that materials and products can withstand thermal stresses without cracking, warping, or losing their functionality.
What is Thermal Shock Testing?
Thermal shock testing involves subjecting a material to sudden temperature variations, typically by alternating between high and low temperatures. This rapid change causes the material to expand and contract unevenly, leading to physical and structural damage if the material is not adequately designed to handle such stress. The test assesses the material’s resistance to cracking, delamination, or other forms of failure caused by thermal expansion and contraction.
The Thermal Shock Process
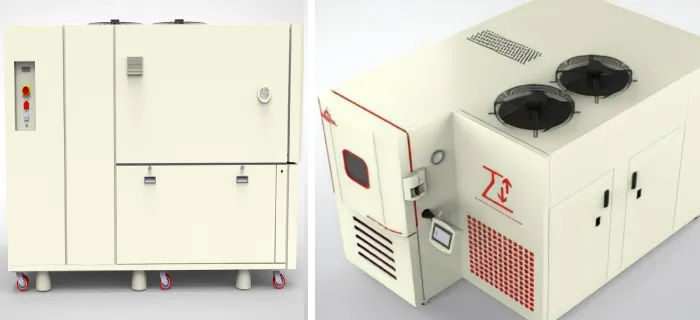
Thermal shock testing typically follows a well-defined process, consisting of the following key stages:
Preparation of Sample: The sample to be tested is first placed inside the thermal shock chamber. It is essential that the sample represents the actual product or material that will undergo real-world conditions. This ensures that the test results are relevant to the product’s anticipated performance.
Temperature Cycling: The sample is subjected to rapid temperature changes, usually between two extreme temperatures—one high and one low. The test may involve step changes (moving quickly from one temperature to another) or cyclic thermal shock (repeated cycling between high and low temperatures). For example, the sample could be exposed to temperatures ranging from -70°C to +80°C, rapidly switching from one extreme to the other. This cycling can happen over minutes, hours, or even days, depending on the test requirements.
Temperature Ramp Rates: The rate at which the temperature changes is critical in thermal shock testing. Fast ramp rates (high-speed temperature transitions) are often used to simulate the quick temperature shifts that occur in real-world environments. These rates can range from a few degrees per minute to several hundred degrees per minute, depending on the product being tested.
Hold Times: After the sample reaches the high or low temperature, it may be held at that temperature for a specified amount of time before switching to the opposite temperature. This ensures that the sample is exposed to the full range of thermal stress during the test.
Observation of Failure: Throughout the test, any signs of failure, such as cracking, warping, delamination, or other material damage, are carefully monitored and recorded. Failures may occur due to thermal expansion or contraction within the material, causing internal stresses that lead to fractures or structural degradation.
Post-Test Analysis: After completing the thermal shock cycles, the sample is removed from the chamber and analyzed in detail. Common methods of analysis include visual inspection, X-ray imaging, and mechanical testing. The results help engineers understand how the material has withstood the thermal stress and whether it is suitable for its intended application.
Purpose of Thermal Shock Testing
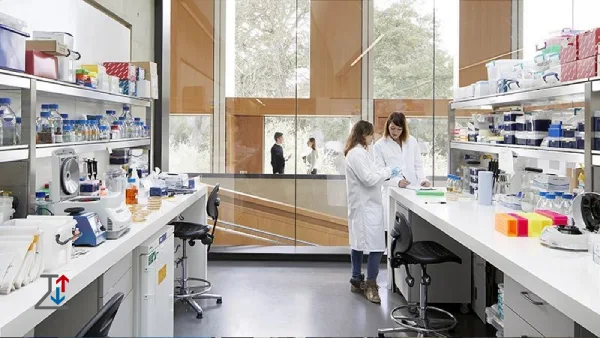
The primary goal of thermal shock testing is to assess the durability of materials under extreme temperature changes, which are common in many industrial, automotive, aerospace, and electronics applications. thermal shock testing is to reproduce real-world scenarios where materials may experience quick temperature changes. By subjecting materials to controlled thermal shock tests, engineers can survey their capacity to resist such conditions and make educated choices for fabric choice, plan optimization, and fabricating forms. By subjecting a material to these stresses in a controlled environment, manufacturers can:
- Predict Material Failure: Thermal shock testing helps identify materials that may fail prematurely under fluctuating temperatures.
- Improve Product Quality: Understanding a material’s behavior during thermal cycling allows manufacturers to refine product designs and select more suitable materials.
- Ensure Safety and Reliability: In industries such as aerospace, automotive, and electronics, materials must perform reliably under extreme temperature conditions to avoid catastrophic failures.
Key Factors in Thermal Shock Testing
Several factors can influence the outcome of thermal shock tests:
- Temperature Range: The severity of the thermal shock is determined by the difference between the high and low temperatures the material experiences. Greater temperature differences typically cause higher stress.
- Test Duration and Cycle Time: The length of time a material is exposed to high and low temperatures, as well as how quickly these transitions occur, can impact its ability to withstand thermal shock.
- Material Properties: Different materials have varying degrees of resistance to thermal shock based on their thermal conductivity, expansion coefficients, and overall brittleness or flexibility.
Common Challenges in Thermal Shock Testing
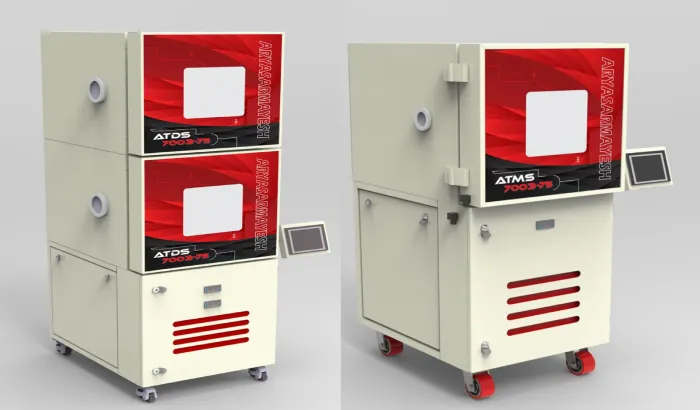
Thermal shock testing plays a critical role in ensuring that materials, components, and products can withstand rapid temperature changes, simulating real-world conditions. However, the process is not without its challenges. These challenges can affect the accuracy of results, the efficiency of testing, and the overall reliability of the product under stress. Below are some of the most common challenges faced during thermal shock testing:
1. Achieving Accurate Temperature Transitions
One of the most significant challenges in thermal shock testing is ensuring that temperature transitions between extremes (hot to cold, or vice versa) occur rapidly and precisely. The temperature change must be uniform across the sample to avoid uneven stresses. Achieving consistent temperature ramps and ensuring that the thermal shock chamber maintains the desired temperature ranges can be difficult. Without this, the results may not accurately reflect real-world conditions, leading to incorrect conclusions about product durability.
2. Managing Sample Size and Configuration
Different materials and components require varying test conditions. For example, larger or irregularly shaped samples may not heat up or cool down as quickly as smaller or more uniform samples, which can lead to uneven thermal stress. The geometry of the sample can significantly influence the results, and testing procedures may need to be adjusted to account for these variations. Ensuring that the sample is adequately prepared for the test and placed correctly in the chamber is crucial for accurate results.
3. Temperature Gradient and Uniformity
The temperature gradient, or the difference in temperature across the material being tested, can also be a challenge. If the thermal shock chamber does not provide an evenly distributed temperature across the sample, this can result in localized failures. For instance, thicker materials may experience differential expansion and contraction, potentially leading to cracking or warping. Achieving uniform temperature distribution across the sample is essential for reliable and reproducible results.
4. Test Duration and Cycle Count
Thermal shock tests often require multiple cycles of temperature changes to simulate long-term exposure. However, performing these cycles over extended periods can be time-consuming and resource-intensive. Many tests can take hours or even days to complete, depending on the material being tested. Moreover, it’s important to ensure that the test duration is sufficient to capture the performance of the material under realistic conditions, without being unnecessarily prolonged, which can be costly.
5. Failure Detection and Analysis
Another challenge in thermal shock testing is the accurate detection and analysis of failures. Failures caused by thermal shock can sometimes be difficult to identify immediately, particularly if they are internal or microscopic. Cracking, delamination, warping, or other material deformations may only become apparent after repeated cycles or post-test analysis. This makes it critical to have the right tools for inspecting and analyzing the sample after the test, such as high-resolution imaging equipment or X-ray systems.
6. Equipment Calibration and Maintenance
Thermal shock testing equipment, such as temperature chambers, needs to be accurately calibrated to ensure consistent and reliable results. Without proper calibration, the test equipment may deliver inaccurate temperature readings or fail to meet industry standards, affecting the test outcomes. Regular maintenance and calibration of thermal shock chambers are essential to avoid malfunctions and ensure that the equipment performs as expected.
7. Material-Specific Challenges
Different materials react to thermal shock in distinct ways. Metals, ceramics, plastics, and composites all have unique thermal expansion rates, which means that they will perform differently under the same conditions. Adapting the testing procedure to account for these material-specific challenges requires expertise and knowledge of how various materials respond to thermal stress. For example, ceramics may crack under thermal shock, while metals may bend or warp. Selecting the appropriate test conditions for each material is crucial.
AryaSarmayesh’s thermal shock chambers
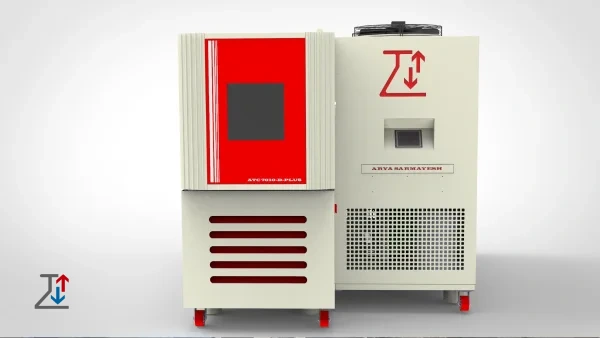
We are at Aryasarmayesh, we understand the challenges that come with thermal shock testing, and we are committed to providing cutting-edge solutions to help you achieve accurate, reliable results. As a leading supplier of thermal shock test chambers, we offer advanced chambers designed to meet the specific needs of your testing requirements.
Our thermal shock test chambers are equipped with state-of-the-art technology, ensuring precise temperature control, rapid cycling, and uniform temperature distribution across your samples. Whether you are testing automotive components, electronics, or materials for aerospace applications, our test chambers are built to provide consistent and repeatable results.
Key features include:
- Advanced Technology: Our thermal shock chambers feature the latest in temperature control and rapid cycling technology, allowing you to test a wide range of materials and components under varying thermal conditions.
- Customization: We offer customizable options to meet the unique needs of your testing procedures. Whether it’s temperature range, chamber size, or cycle time, we can tailor a solution to fit your requirements.
- Reliability: With rigorous testing and quality assurance, our thermal shock test chambers are built for long-term performance and reliability, helping you reduce the challenges associated with equipment failure or inconsistent results.
- Expert Support: Our team of experts is always available to assist you with setup, calibration, and troubleshooting. We provide comprehensive training and support to ensure you get the most out of your thermal shock testing.
- Cost-Effective Solutions: We offer competitive pricing without compromising on quality, making advanced thermal shock testing accessible for companies of all sizes.
- Durability Testing: Ensure the longevity and reliability of materials and components subjected to extreme environmental stress.
- Customizable Solutions: Tailor the chamber specifications to your testing requirements for maximum efficiency.
- Energy-Efficient Design: Designed with advanced energy-saving technologies without compromising performance.
Partner with Aryasarmayesh to enhance the efficiency and accuracy of your thermal shock testing. Our test chambers are trusted by industries worldwide to meet rigorous standards and deliver superior results. Contact us today to learn more about how we can help you overcome the challenges of thermal shock testing with the best equipment on the market.
For a free consultation with our experts, please contact us.
The mechanics of thermal shock testing
The mechanics of thermal shock testing rely on specialized equipment known as environmental chambers, which are capable of precisely controlling temperature conditions. These chambers are outlined to quickly move between extraordinary temperature ranges, frequently traversing from well underneath solidifying to a few hundred degrees Celsius. Inside these chambers, examples are carefully put and uncovered to foreordained thermal shock testing, which may comprise of quick shock followed by quick cooling, or bad habit versa.
Amid the testing handle, a few key variables come into play to guarantee exact and dependable results. Firstly, the rate of temperature alteration is carefully controlled to imitate real-world conditions as closely as conceivable. This makes a difference in duplicating the thermal shock that materials may encounter amid the utilization or presentation of natural variables. Furthermore, the term and number of warm stun cycles are optimized based on industry benchmarks and particular application necessities.
Thermal Shock Testing vs. Other Testing Methods
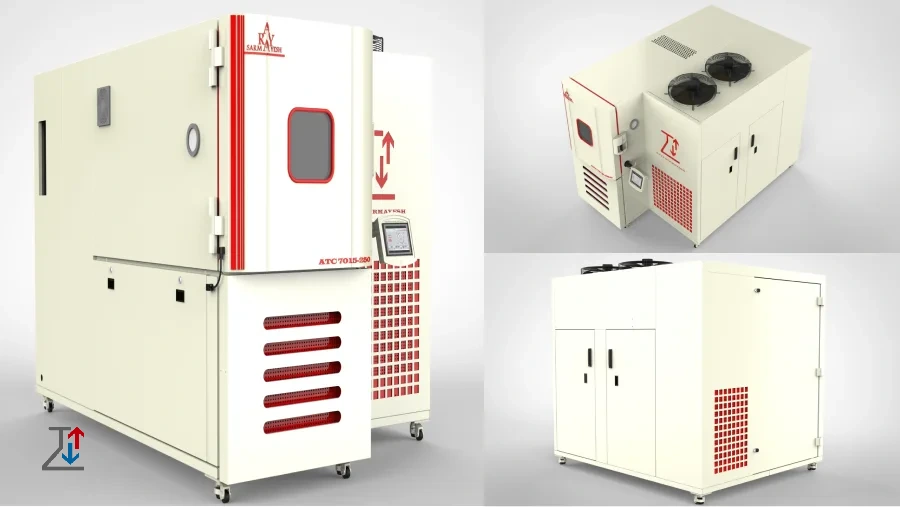
When it comes to evaluating the durability, reliability, and performance of materials and components under extreme environmental conditions, various testing methods are employed. Each testing method serves specific purposes depending on the type of stress or conditions a product will face during its lifecycle. One important test is thermal shock testing, which assesses how materials or products handle rapid temperature changes. However, thermal shock testing is just one method in the broader field of environmental testing. In this article, we compare thermal shock testing with other common testing methods to highlight their differences, advantages, and limitations.
1. Thermal Shock Testing
Thermal shock testing involves exposing materials or components to rapid and extreme temperature changes, typically cycling between hot and cold temperatures. This type of testing simulates real-world conditions where products may experience sudden shifts in temperature, such as when electronics are exposed to outdoor environments or when automotive parts face fluctuating temperatures due to engine operations.
Key Characteristics:
- Temperature Cycling: Rapid transitions between high and low temperatures.
- Simulates Real-World Conditions: Useful for products subjected to frequent or extreme temperature changes.
- Focus on Material Behavior: Primarily measures the material’s ability to withstand thermal expansion and contraction.
Applications:
- Electronics (e.g., circuit boards)
- Automotive components
- Aerospace materials
- Industrial machinery
Advantages:
- Identifies Structural Failures: Helps detect cracking, warping, or delamination due to thermal stress.
- Simulates Harsh Conditions: Provides insight into how materials react under extreme temperature fluctuations.
Limitations:
- Doesn’t Assess Long-Term Wear: It focuses on immediate failures from temperature shifts, not the gradual wear and tear over time.
- May Not Simulate Other Environmental Stresses: Thermal shock testing alone cannot replicate the combination of factors like humidity or mechanical stress.
2. Accelerated Life Testing (ALT)
Accelerated life testing is designed to simulate long-term wear and aging of a product in a short amount of time by stressing the product with extreme conditions, such as higher temperatures, humidity, or mechanical stress. The goal is to predict the product’s lifespan and performance degradation.
Key Characteristics:
- Extended Stress Exposure: Products are subjected to accelerated stress for short durations.
- Focus on Longevity: Measures how the product’s performance degrades over time under harsh conditions.
Applications:
- Consumer electronics
- Automotive parts
- Batteries
- Medical devices
Advantages:
- Long-Term Prediction: Provides a clearer picture of how a product will behave over its lifespan.
- Holistic Testing: Often involves multiple environmental stresses (temperature, humidity, vibration).
Limitations:
- Time-Consuming: Even though the test is accelerated, it may still take several hours or days to complete, depending on the conditions being simulated.
- Less Focus on Immediate Failures: It may not provide insight into immediate catastrophic failures like thermal shock testing.
3. Thermal Cycling Testing
Thermal cycling testing is similar to thermal shock testing but involves a more gradual temperature transition. Instead of rapid shifts, the temperature changes slowly, allowing the material to acclimate to the new conditions. Thermal cycling is used to simulate long-term exposure to temperature fluctuations over an extended period.
Key Characteristics:
- Gradual Temperature Shifts: The temperature change is typically slower than in thermal shock testing.
- Repetitive Cycles: The product undergoes repeated cycles of heating and cooling.
Applications:
- Solder joints in electronics
- Aerospace components
- Automotive testing (e.g., exhaust systems)
Advantages:
- Simulates Long-Term Temperature Fluctuations: Ideal for testing components that will be exposed to frequent, but not necessarily sudden, temperature changes.
- Less Stressful than Thermal Shock: Since the temperature shifts are gradual, this test tends to be less extreme than thermal shock testing.
Limitations:
- May Not Detect Immediate Failures: Unlike thermal shock testing, the slower temperature changes may not cause the immediate failures that would reveal weaknesses in materials or components.
- Limited to Cyclic Stress: It doesn’t simulate the more severe, sudden temperature extremes that may occur in real-world applications.
4. Environmental Testing
Environmental testing involves exposing a product to a combination of factors that simulate real-world environmental conditions, including temperature, humidity, vibration, and pressure. Environmental tests are typically more comprehensive and can involve any combination of these factors to assess the overall performance and durability of a product in a specific environment.
Key Characteristics:
- Multi-Factor Stress Testing: Simulates a combination of real-world environmental conditions, such as high humidity and temperature changes, mechanical stress, etc.
- Holistic Approach: Focuses on a product’s ability to perform in real-world environments.
Applications:
- Outdoor equipment
- Military and defense products
- Electronics used in varying climates
Advantages:
- Realistic Simulation: Provides a comprehensive assessment of how products will perform in real-life conditions.
- Comprehensive Durability Insights: Helps assess performance under multiple stresses (temperature, humidity, vibration, etc.).
Limitations:
- More Complex and Time-Consuming: Environmental testing is often more complex to set up and requires more time to complete compared to thermal shock testing alone.
- More Expensive: Requires sophisticated equipment and a combination of testing chambers and sensors.
5. Vibration Testing
Vibration testing subjects a product to mechanical vibrations to simulate the stresses it might experience during transportation or use. Vibration can mimic real-world conditions like the shock and vibration a component might experience in vehicles or industrial machinery.
Key Characteristics:
- Focus on Mechanical Stress: Measures how components withstand mechanical vibrations and shocks.
- Often Used in Combination: Frequently combined with environmental or thermal testing to assess the impact of vibration in varying conditions.
Applications:
- Automotive parts
- Aerospace components
- Electronics and mobile devices
Advantages:
- Simulates Mechanical Stress: Useful for products that will experience physical vibrations, such as in vehicles, aircraft, or machinery.
- Can Be Combined with Other Tests: Vibration testing can be combined with thermal or environmental tests for a more thorough evaluation.
Limitations:
- Doesn’t Assess Thermal Stress: Vibration testing does not focus on temperature-related failures, so it is less effective for evaluating materials prone to thermal shock.
- Limited to Physical Vibration: Does not simulate environmental factors like humidity or temperature changes.
Benefits of Thermal Shock Testing
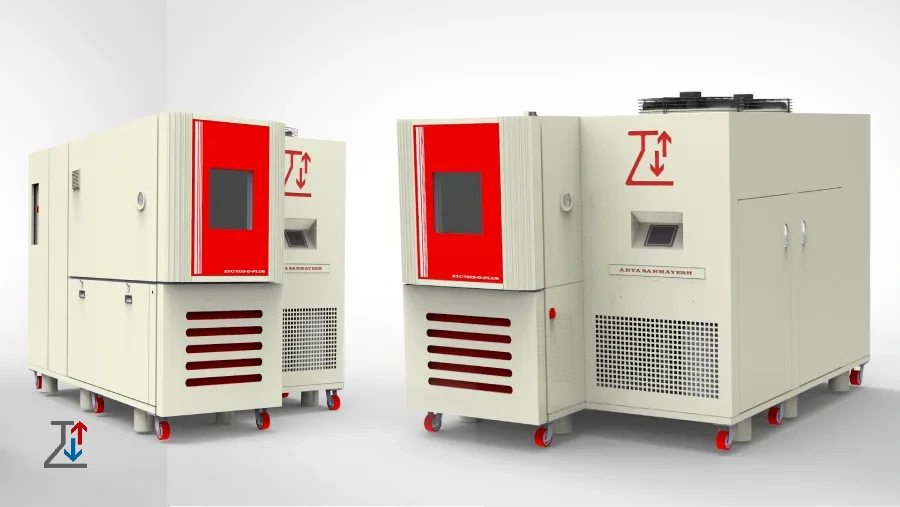
Thermal shock testing is an essential tool for assessing the resilience of materials and components in the face of rapid and extreme temperature changes. Whether in the aerospace, automotive, electronics, or manufacturing sectors, understanding how a material behaves under thermal stress is crucial for product development, performance, and safety. As industries continue to innovate and push the boundaries of material science, thermal shock testing will remain a key factor in ensuring that products can meet the demanding conditions of the real world.
- Reliability Assurance
- Design Optimization
- Cost Savings
- Compliance and Certification
Uncover weaknesses by this thermal testing
The viability of thermal shock testing lies in its capacity to uncover vulnerabilities in materials that might something else go unnoticed. By simulating rapid temperature transitions, engineers can uncover weaknesses, refine designs, and ultimately produce products that excel in the face of real-world challenges.
This important understanding empowers them to refine fabric compositions, optimize item plans, and upgrade fabricating forms to guarantee the most noteworthy levels of execution and unwavering quality.
Thermal Shock Test Standards and Regulations
To ensure consistency, accuracy, and safety, thermal shock testing is governed by various international standards and regulations. Thermal Chamber Standards provide guidelines for conducting tests, interpreting results, and ensuring that products meet specific requirements for different industries.
- ASTM Standards
- ISO Standards
- MIL-STD (Military Standards)
- IEC (International Electrotechnical Commission) Standards
- UL Standards
- Other Industry-Specific Standards
Exploring the Diverse Applications of Thermal Shock Testing
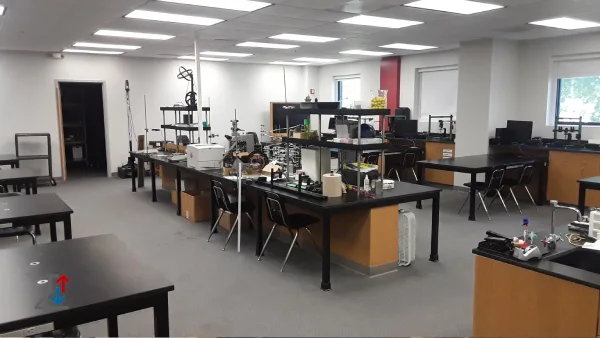
Thermal shock testing, a method to evaluate how materials and products respond to sudden temperature changes, plays a critical role across various industries.
In following delves into the multifaceted applications of thermal shock testing across different sectors.
- Electronics Industry: Thermal shock testing guarantees the unwavering quality of semiconductors, printed circuit sheets, and other electronic parts by mimicking temperature moves, hence distinguishing potential shortcomings and guaranteeing strength against warm push.
- Automotive Sector: Thermal shock testing is instrumental in confirming the solidness of materials utilized in vehicles, guaranteeing they can withstand extraordinary conditions without corruption. This testing makes a difference producers upgrade the life span and execution of car components, eventually moving forward vehicle unwavering quality.
- Aerospace Applications: By subjecting materials to rapid temperature changes, engineers can identify potential failures and design more resilient aerospace systems.
- Glass and Ceramics: Crystal, cookware, and ceramic components experience warm cycling to survey their resistance to sudden temperature varieties. This testing helps prevent premature failure and ensures product safety and reliability.
- Consumer Goods: Thermal shock testing confirms the strength of these items, guaranteeing they meet quality benchmarks and perform dependably beneath shifting natural conditions.
- Defense and Military Applications: By subjecting materials to thermal shock cycling, engineers can distinguish vulnerabilities and plan military gear capable of withstanding unforgiving situations.
- Therapeutic Gadget Industry: This testing is basic for guaranteeing the unwavering quality and execution of basic healthcare hardware.
Conclusion:
For those seeking high-quality thermal shock testing equipment, Aryasarmayesh offers state-of-the-art thermal shock chambers that provide precise and reliable testing solutions. Our equipment ensures consistent and rapid temperature transitions, helping you identify weaknesses and improve the design of your products. Trust Aryasarmayesh to provide the technology you need for accurate thermal shock testing, so you can create products that perform reliably under extreme conditions. Contact us today to learn more about our thermal shock test chambers and how they can support your testing needs.
Related articles in Aryasarmayesh: