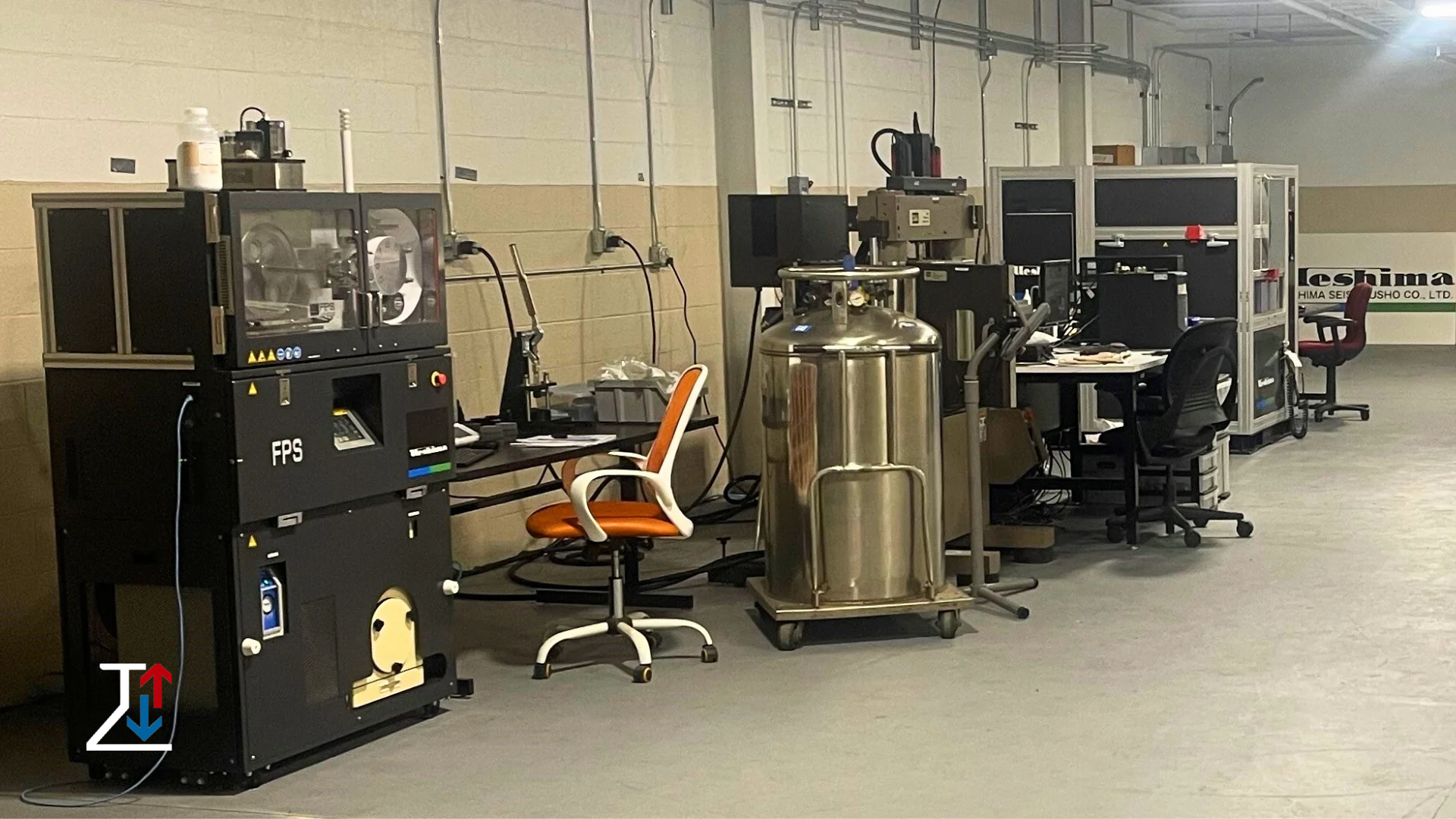
Industrial test chambers are essential tools across a variety of industries, including automotive, electronics, pharmaceuticals, aerospace, and consumer goods. These test chambers allow companies to rigorously test their products under controlled environmental conditions, ensuring they can withstand various real-world stresses before being introduced to the market. This article explores what industrial test chambers are, the types available, their uses, and key considerations for choosing the right one for specific testing requirements.
What is an Industrial Test Chamber?
An industrial test chamber is a controlled environment designed to simulate various conditions, such as extreme temperatures, humidity, altitude, vibration, and light exposure. They are used to assess a product’s reliability, performance, and durability by subjecting it to conditions that mimic actual or accelerated environments the product might encounter. This helps manufacturers predict how products will respond to wear, aging, and potentially harsh conditions, enabling improvements before mass production.
Types of Industrial Test Chambers
Several industrial test chambers are available, each serving a specific purpose. Common categories include:
UV Chambers
UV Chambers simulate exposure to sunlight (UV radiation) and other environmental factors, such as rain, wind, and dust. UV and weathering chambers are used in industries like construction, automotive, and packaging to ensure products can endure prolonged exposure to outdoor conditions.
Temperature and Humidity Chambers
Temperature and Humidity Chambers are among the most widely used types. Temperature chambers can control temperatures ranging from sub-zero to extremely high levels, while humidity chambers maintain a specific level of moisture in the air. Combined temperature and humidity chambers test how products respond to various temperature and moisture levels, important in industries like electronics and pharmaceuticals.
Thermal Shock Chambers
Thermal shock chambers rapidly alternate between extreme hot and cold temperatures to test products’ resilience under abrupt temperature changes. These chambers are essential in automotive, aerospace, and electronics industries, where products may experience sudden temperature shifts.
Vibration Test Chambers
Vibration Test Chambers combine temperature control with mechanical vibration to evaluate a product’s structural integrity and durability. Vibration chambers are essential in industries like automotive and aerospace, where components must endure constant movement or shocks during operation.
Altitude Test Chambers
Altitude chambers simulate high-altitude conditions, including reduced air pressure, which can affect electronics, batteries, and other sensitive components. They are commonly used in aerospace, military, and automotive testing.
Corrosion Test Chambers
Corrosion test chambers, also known as salt spray or salt fog chambers, expose materials to salt or other corrosive agents to test their resistance to rust and other forms of corrosion. This is particularly important for materials exposed to harsh environments, such as marine or industrial settings.
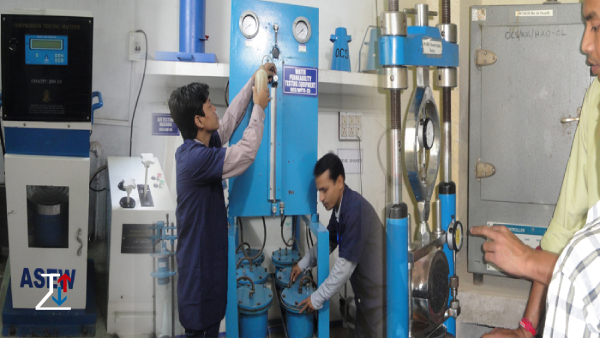
Applications of Industrial Test Chambers
Industrial test chambers have applications across various industries, such as:
- Automotive and Aerospace: Testing vehicle and aircraft parts for temperature, vibration, altitude, and corrosion resilience ensures that components are durable and safe.
- Electronics: Electronic devices are subjected to thermal, humidity, and vibration tests to ensure they function consistently across different environments.
- Pharmaceuticals: Stability and shelf-life testing are crucial for ensuring the efficacy and safety of drugs, which require precise temperature and humidity conditions.
- Consumer Goods: Test chambers help validate the durability and longevity of household appliances, packaging, and other goods by simulating real-life usage and environmental conditions.
- Construction Materials: UV, humidity, and salt spray tests simulate outdoor exposure to ensure materials used in building are resilient against weathering and corrosion.
Key Considerations When Choosing an Industrial Test Chamber
Industrial test chambers have Considerations, such as:
Test Requirements
Define the specific tests needed. For instance, a thermal shock chamber is ideal if the product requires extreme temperature shifts. However, if you need to test for a combination of temperature and vibration, then a chamber equipped to handle both conditions should be prioritized.
Size and Capacity
Test chambers come in various sizes, from compact, benchtop models for small samples to large walk-in chambers for bigger components or assemblies. Choosing the right size depends on the type and volume of products being tested.
Control and Monitoring Features
Modern test chambers come with advanced control and monitoring systems, often digital or touchscreen interfaces, for precise adjustments. Some chambers also have data logging and remote monitoring capabilities, making it easier to track and analyze results.
Environmental Range
Consider the range of environmental conditions the chamber can replicate, such as temperature range, humidity level, and altitude capacity. Chambers with broader ranges tend to be more versatile but may also come at a higher cost.
Durability and Materials
Industrial test chambers should be constructed from high-quality, corrosion-resistant materials, especially if testing will expose the chamber to corrosive agents, moisture, or extreme conditions.
Safety and Compliance
Many industries have regulatory requirements regarding product testing. Choose a chamber that meets these safety standards and certifications, ensuring the equipment complies with industry regulations.
Energy Efficiency
Industrial test chambers can be energy-intensive, especially those that simulate extreme conditions. Energy-efficient models can reduce long-term operational costs and support sustainability goals.
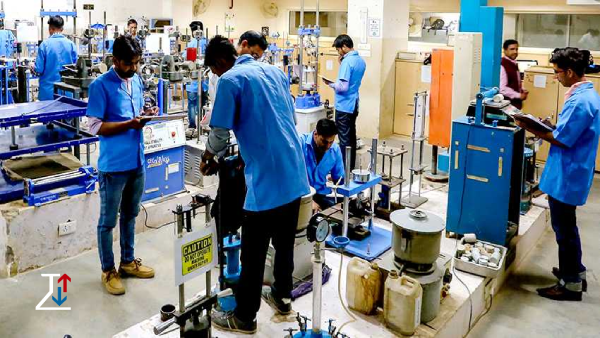
Benefits of Using Industrial Test Chambers
- Enhanced Product Quality: Industrial test chambers provide a thorough assessment, helping manufacturers identify potential weaknesses and enhance product quality before launch.
- Compliance with Standards: Many industries require compliance with regulatory standards. Testing in controlled environments ensures products meet these safety and quality requirements.
- Cost Savings: By identifying and correcting potential issues early in the design or production phase, companies avoid costly recalls and repairs later.
- Increased Consumer Trust: Rigorous testing increases consumer confidence in the durability and reliability of products, enhancing brand reputation.
- Accelerated R&D: Test chambers allow for accelerated life testing, helping companies bring products to market faster by simulating years of wear and tear in a shorter period.
Conclusion
Industrial test chambers are indispensable in modern manufacturing, ensuring that products meet high standards of quality, safety, and durability. With a wide range of test chambers available, companies can find the right solution tailored to their specific testing needs. Investing in the right test chamber not only supports product quality but also reduces costs, strengthens compliance, and accelerates development processes, providing a competitive advantage in today’s demanding markets.
Related articles in Aryasarmayesh: