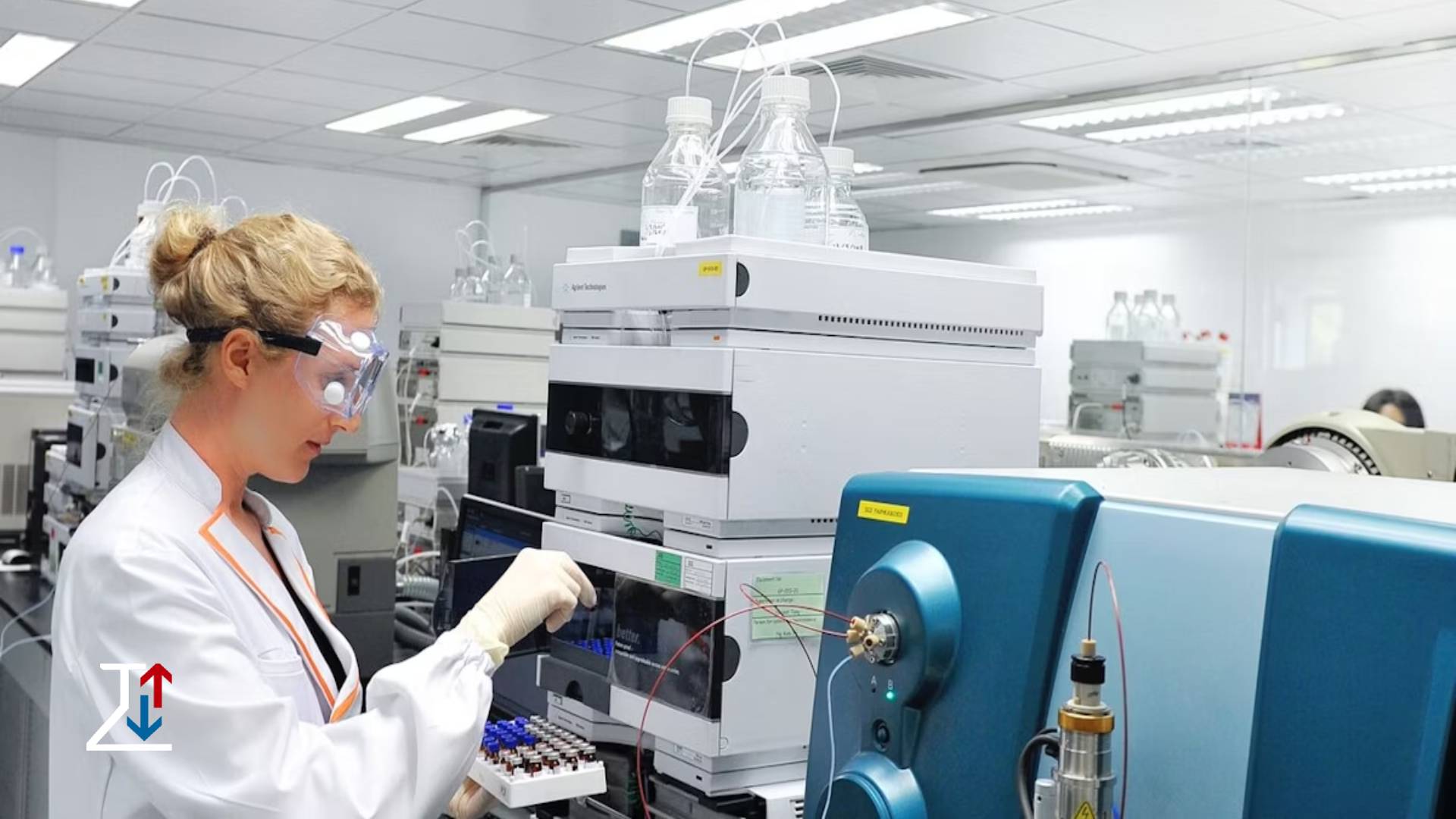
In many industries, accuracy and precision are paramount, especially when dealing with highly sensitive equipment. One of the essential tools for ensuring that instruments perform as expected is the test chamber for calibration. These chambers provide a controlled environment to test and calibrate equipment, allowing for accurate performance measurements under various conditions. This article explores the importance of test chambers in calibration, their types, and how they contribute to reliable and consistent results in numerous sectors.
What is a Test Chamber for Calibration?
A test chamber for calibration is a specially designed, enclosed space where instruments, devices, and equipment are placed for testing and calibration. These chambers are equipped with systems that can simulate various environmental conditions, such as temperature, humidity, pressure, and other factors. By exposing the equipment to these conditions, technicians can evaluate how well the device performs and make necessary adjustments or calibrations to ensure it meets required standards.
The purpose of these test chambers is to provide a controlled environment that mirrors the conditions in which the equipment will be used in the real world. Whether testing a thermocouple, pressure sensor, or humidity gauge, the test chamber helps to verify that the instrument functions correctly and within tolerances.
Types of Test Chambers for Calibration
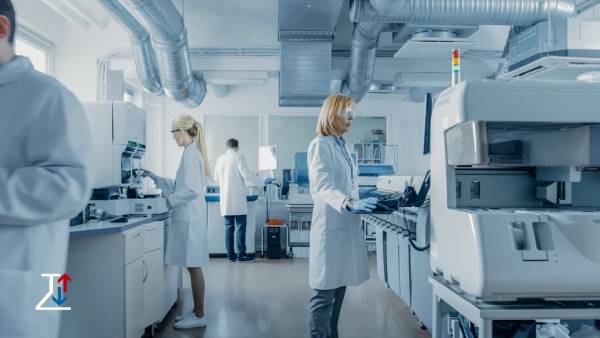
Temperature Test Chambers
Temperature Test chambers are used to test and calibrate temperature-sensitive equipment. They can simulate a wide range of temperatures, from extreme cold to high heat. Temperature test chambers are vital in industries such as electronics, automotive, and aerospace, where equipment must function accurately across various temperature conditions.
Humidity Test Chambers
Humidity test chambers simulate specific humidity levels, often in conjunction with temperature variations. These chambers are used to calibrate sensors that measure humidity or assess how devices perform in humid conditions. Applications include testing HVAC systems, electronic devices, and environmental monitoring instruments.
Thermal Shock Test Chambers
Thermal shock chambers are used to expose equipment to rapid temperature changes, which can cause material stress or failure. These chambers are particularly important for testing components that must endure extreme and rapid shifts in temperature, such as those found in automotive or aerospace applications.
Vibration Test Chambers
These chambers simulate the vibrations that equipment might experience during transport or operation, especially in environments like the automotive, aviation, and military sectors. Vibration testing is critical for ensuring that sensitive instruments and parts do not fail under real-world conditions.
Environmental Test Chambers
Combining several factors such as temperature, humidity, and pressure, these chambers provide a comprehensive testing environment for calibration purposes. They are used in industries that require equipment to perform consistently in varying environmental conditions, like medical devices or food storage equipment.
Pressure Test Chambers
Pressure test chambers are used to calibrate equipment like pressure sensors and gauges. They simulate varying levels of atmospheric pressure or test devices under high-pressure conditions to ensure their accuracy and reliability in critical applications.
Importance of Test Chambers for Calibration
Ensuring Accuracy and Precision
Calibration is essential to ensure that measuring instruments give accurate readings. Without proper calibration, instruments may give false or inconsistent readings, leading to errors in production, research, or safety. Test chambers create a controlled environment in which devices can be calibrated against known standards, ensuring they perform as expected.
Compliance with Industry Standards
Many industries have strict standards for accuracy, especially those related to safety, health, and manufacturing. Test chambers help companies meet these regulatory requirements, ensuring that their equipment is up to code and compliant with national and international standards (such as ISO or ANSI).
Reducing Downtime and Improving Reliability
By calibrating instruments in test chambers regularly, companies can identify issues before they lead to equipment failure. This proactive approach helps reduce unexpected downtimes, extending the life of equipment, and improving reliability in operations.
Optimizing Performance
Proper calibration ensures that instruments operate at peak performance, enhancing the overall quality of products or services. In industries like pharmaceuticals, electronics, and aerospace, even minor discrepancies in measurement can lead to significant quality issues. Test chambers enable technicians to fine-tune equipment, ensuring maximum efficiency.
The Calibration Process in a Test Chamber
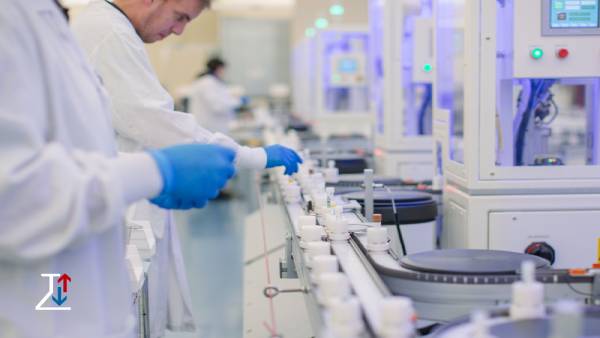
Preparing the Equipment
The first step in the calibration process is to prepare the equipment being tested. This involves ensuring that the device is clean, correctly set up, and ready for testing.
Setting Environmental Parameters
Based on the type of equipment, the test chamber’s environmental conditions are adjusted to replicate the conditions under which the device will operate. For example, a temperature sensor may be tested in a chamber set to different temperature points, or a pressure sensor may be tested under varying atmospheric pressures.
Running the Test
The equipment is then placed inside the test chamber, and measurements are taken. These readings are compared to known standards to determine the accuracy of the instrument. Depending on the results, adjustments may be made to bring the equipment within the desired tolerance range.
Adjustments and Calibration
If the instrument is found to be inaccurate, technicians will adjust it accordingly, ensuring it meets the required specifications. In some cases, recalibration may involve resetting or replacing parts of the equipment.
Final Verification and Documentation
Once the calibration is complete, the equipment is tested again to confirm the adjustments have been successful. A detailed report is often generated to document the calibration process, which can be crucial for regulatory compliance and future reference.
Applications of Test Chambers for Calibration
Test chambers for calibration are widely used in various industries, including:
- Aerospace: Testing instruments that need to withstand extreme conditions during flight, such as pressure sensors, temperature sensors, and accelerometers.
- Automotive: Calibrating components like pressure sensors, temperature gauges, and other monitoring devices that operate in vehicles.
- Pharmaceutical: Ensuring that equipment used in drug manufacturing and testing is accurately calibrated for compliance with strict health regulations.
- Electronics: Testing devices such as thermistors, humidity sensors, and other electronics components to ensure their precision in a variety of environments.
- Manufacturing: Verifying the accuracy of measurement instruments that are used in production processes, such as scales, meters, and gauges.
Conclusion
Test chambers for calibration are indispensable tools in ensuring that equipment and instruments meet the highest standards of accuracy and reliability. By simulating real-world conditions and providing a controlled testing environment, these chambers help to maintain the precision of instruments across a wide range of industries. Regular calibration in these chambers not only guarantees compliance with industry standards but also improves equipment longevity and performance. As technology advances and industries demand even higher precision, the role of test chambers in calibration will continue to grow in importance.
Read more:
The Importance of Heat and Cold Test Chambers
Xenon Test Chambers