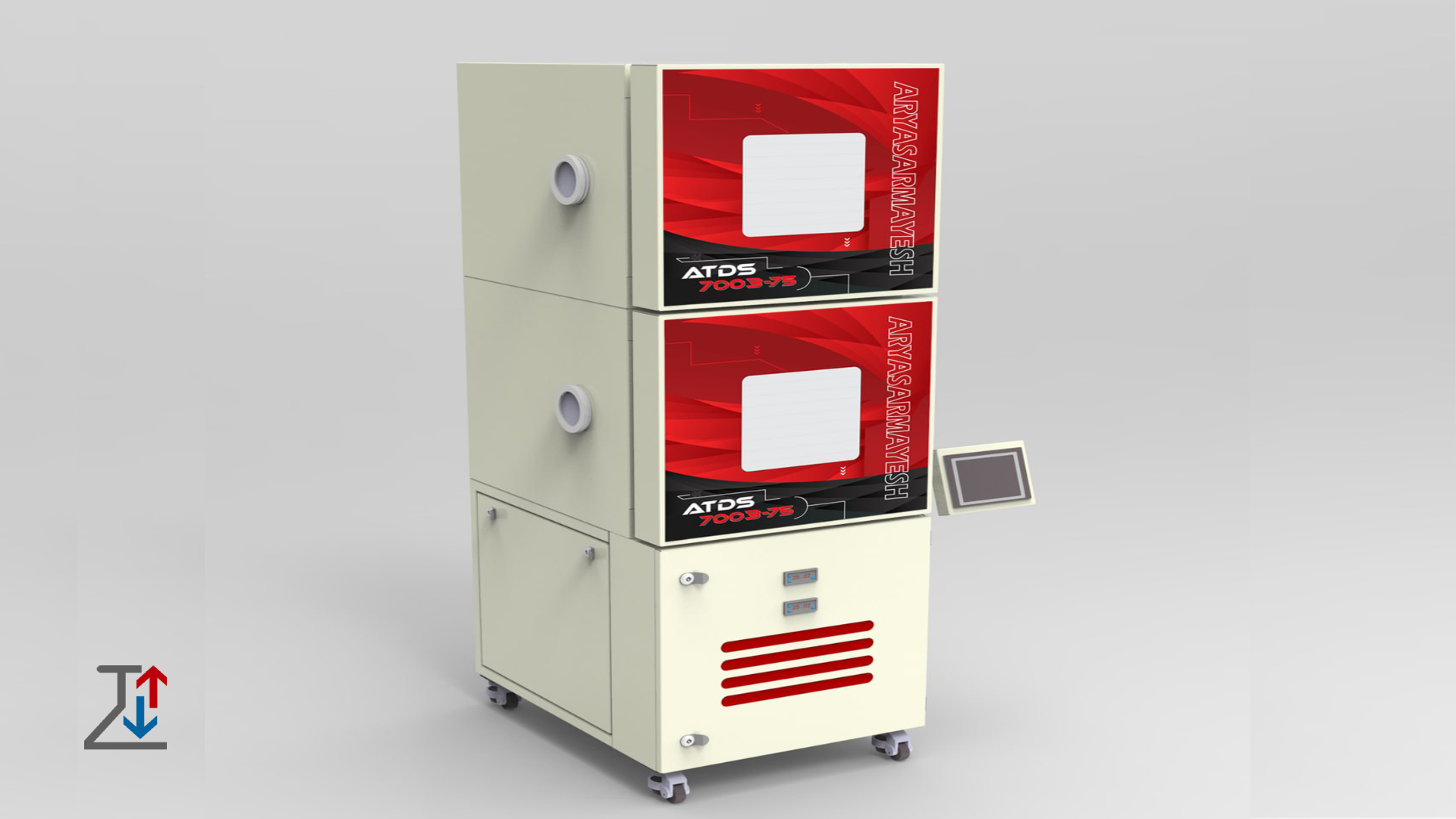
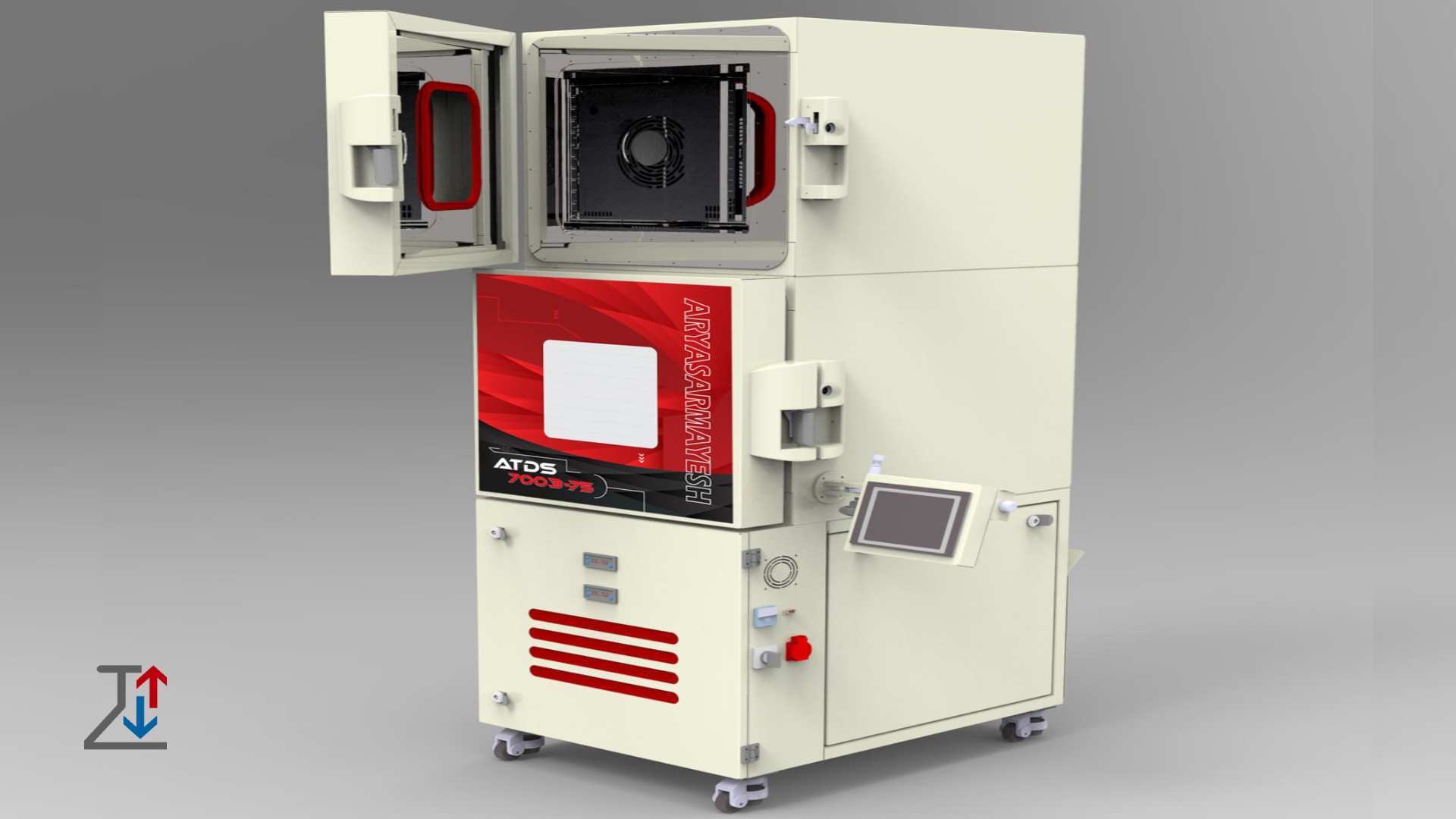

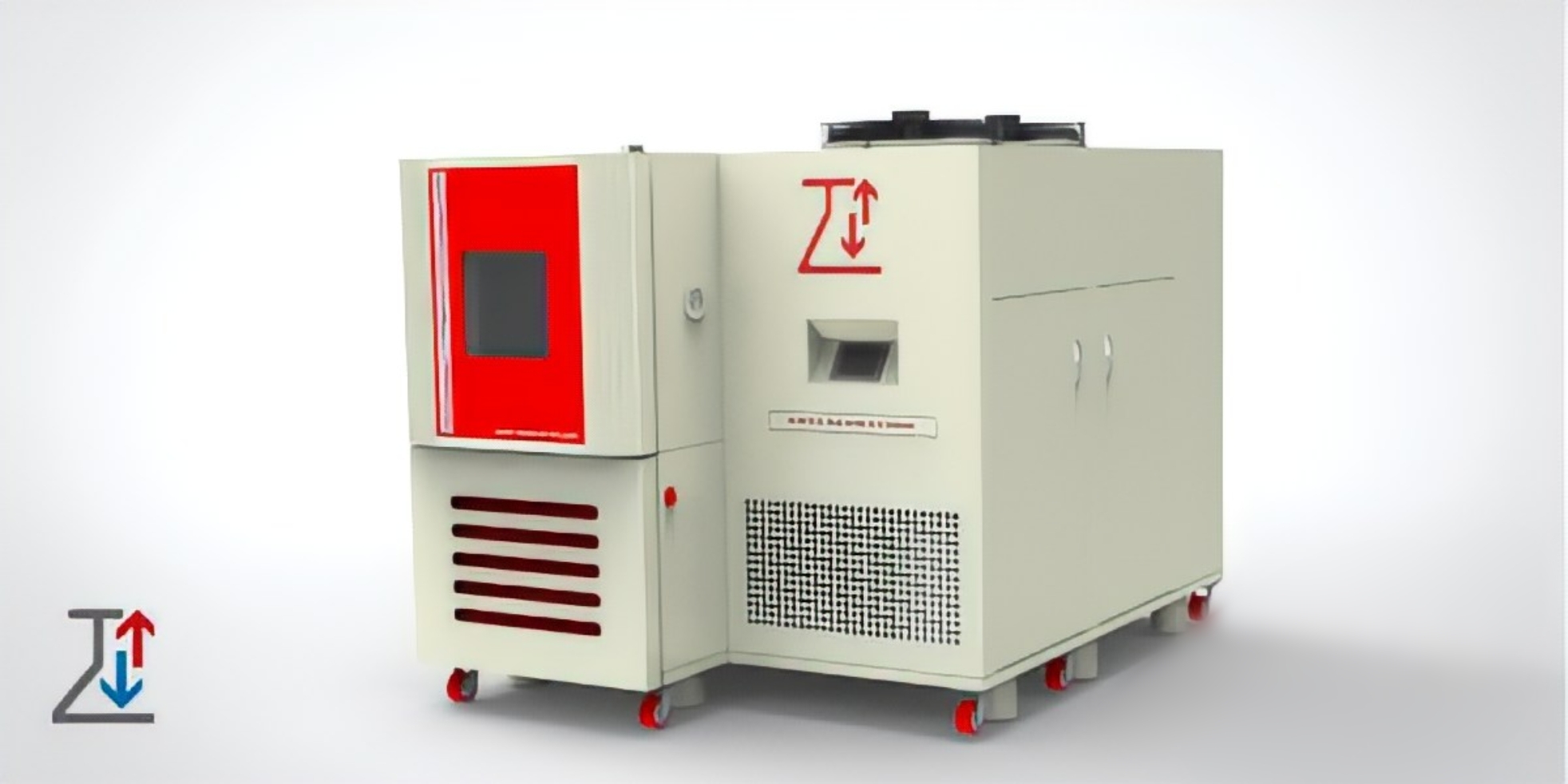
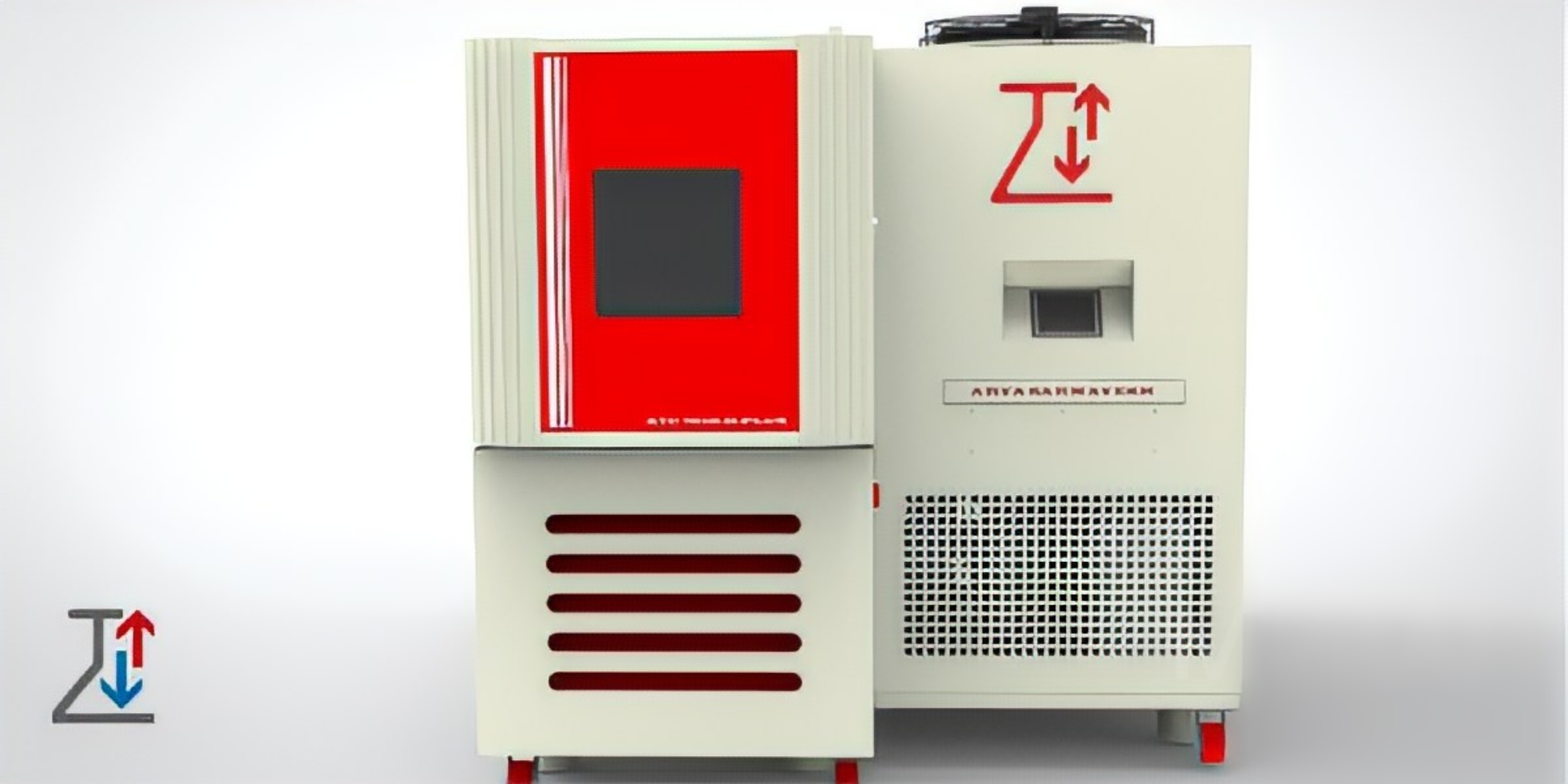
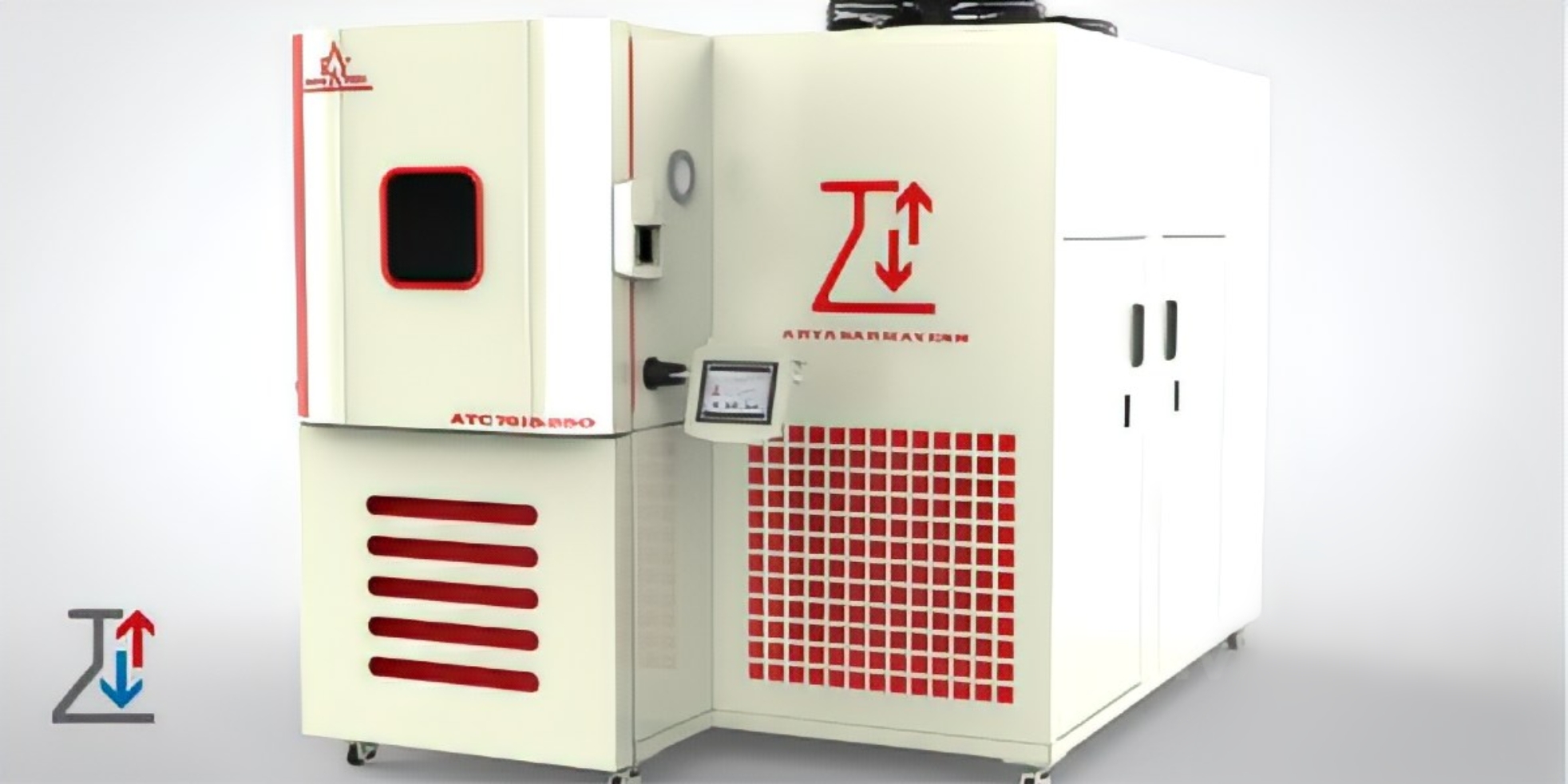
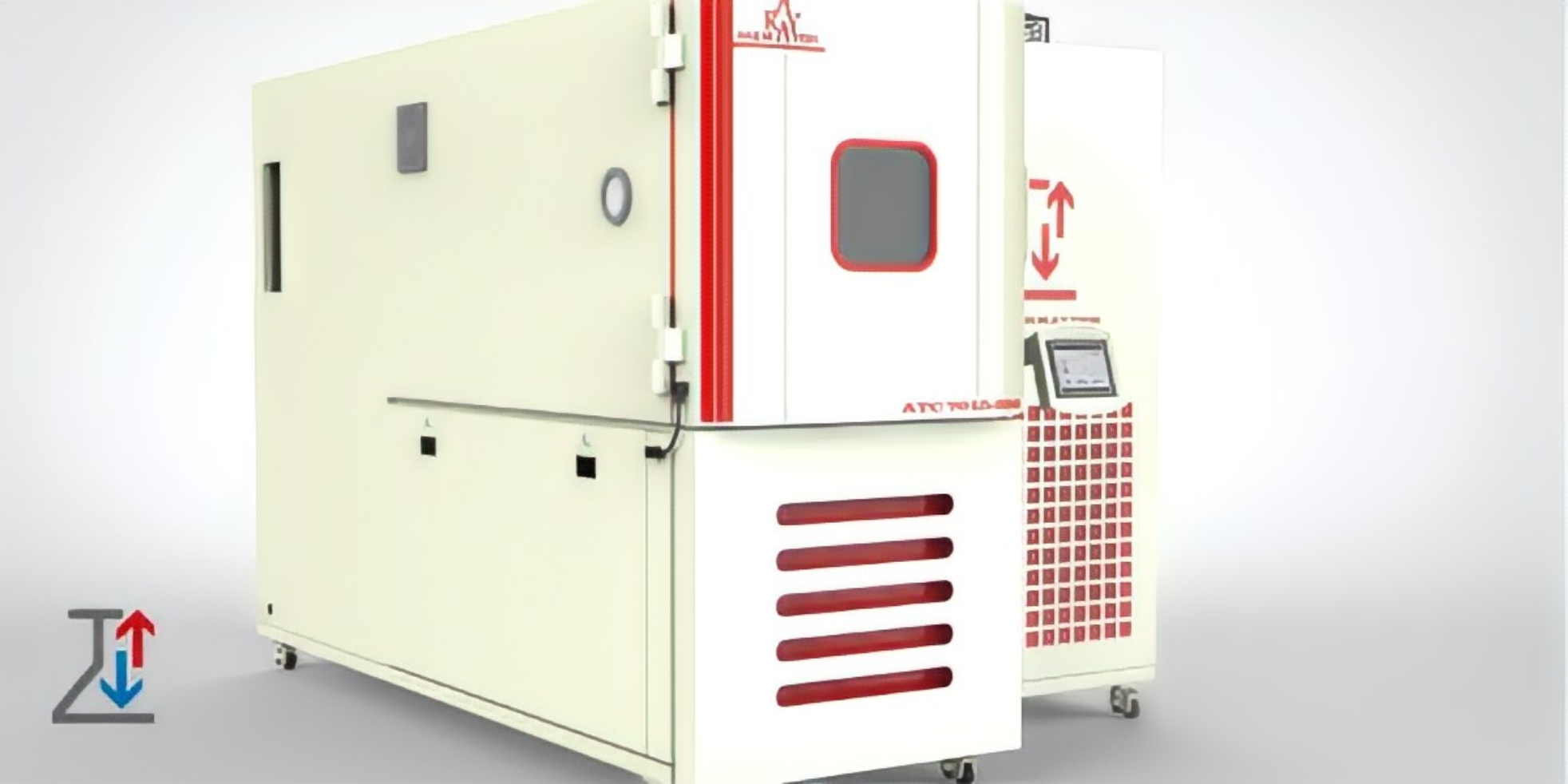
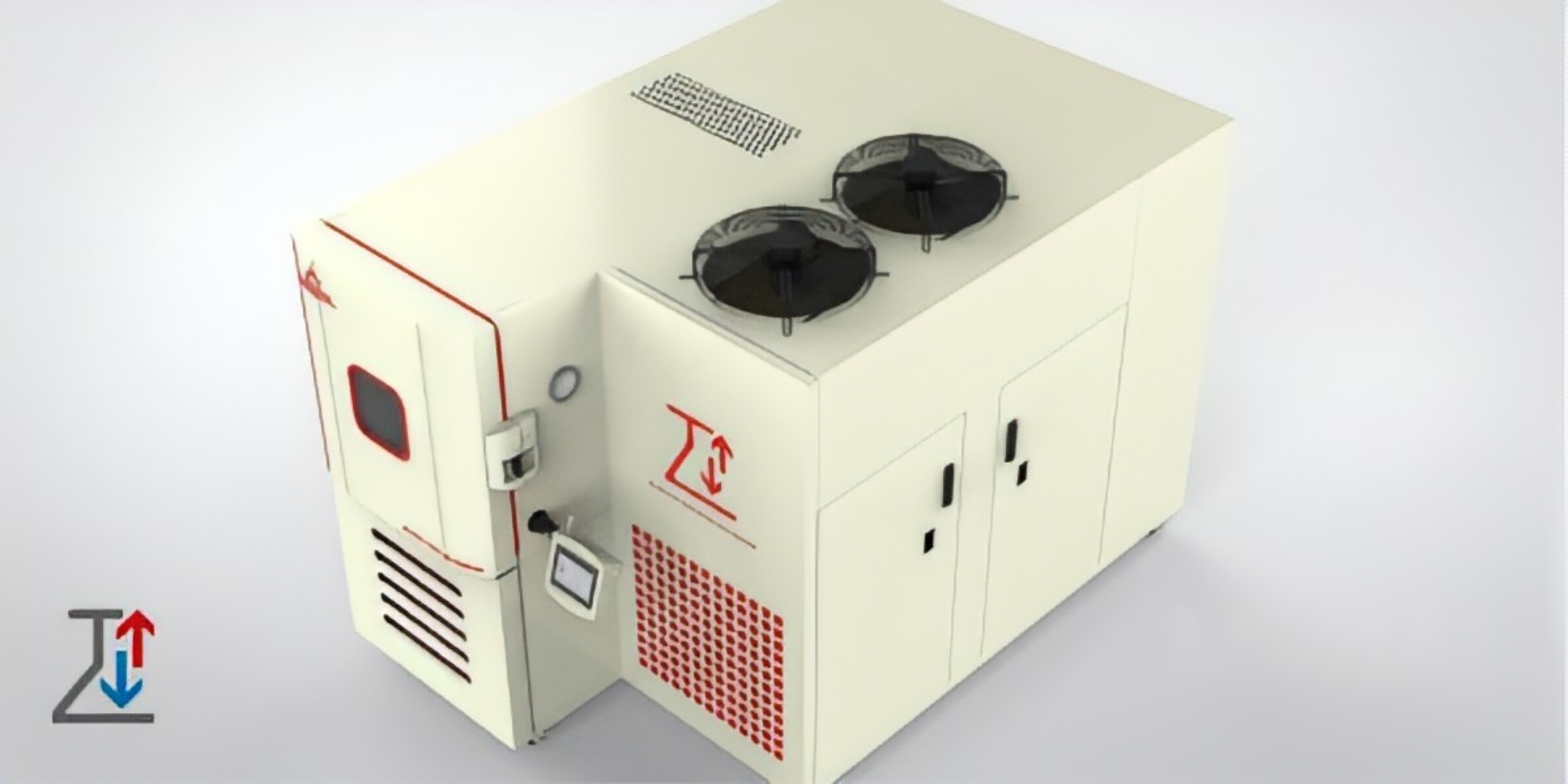
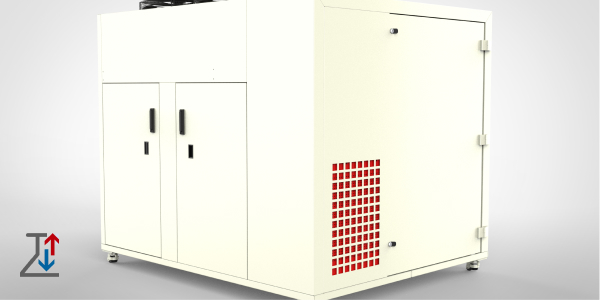
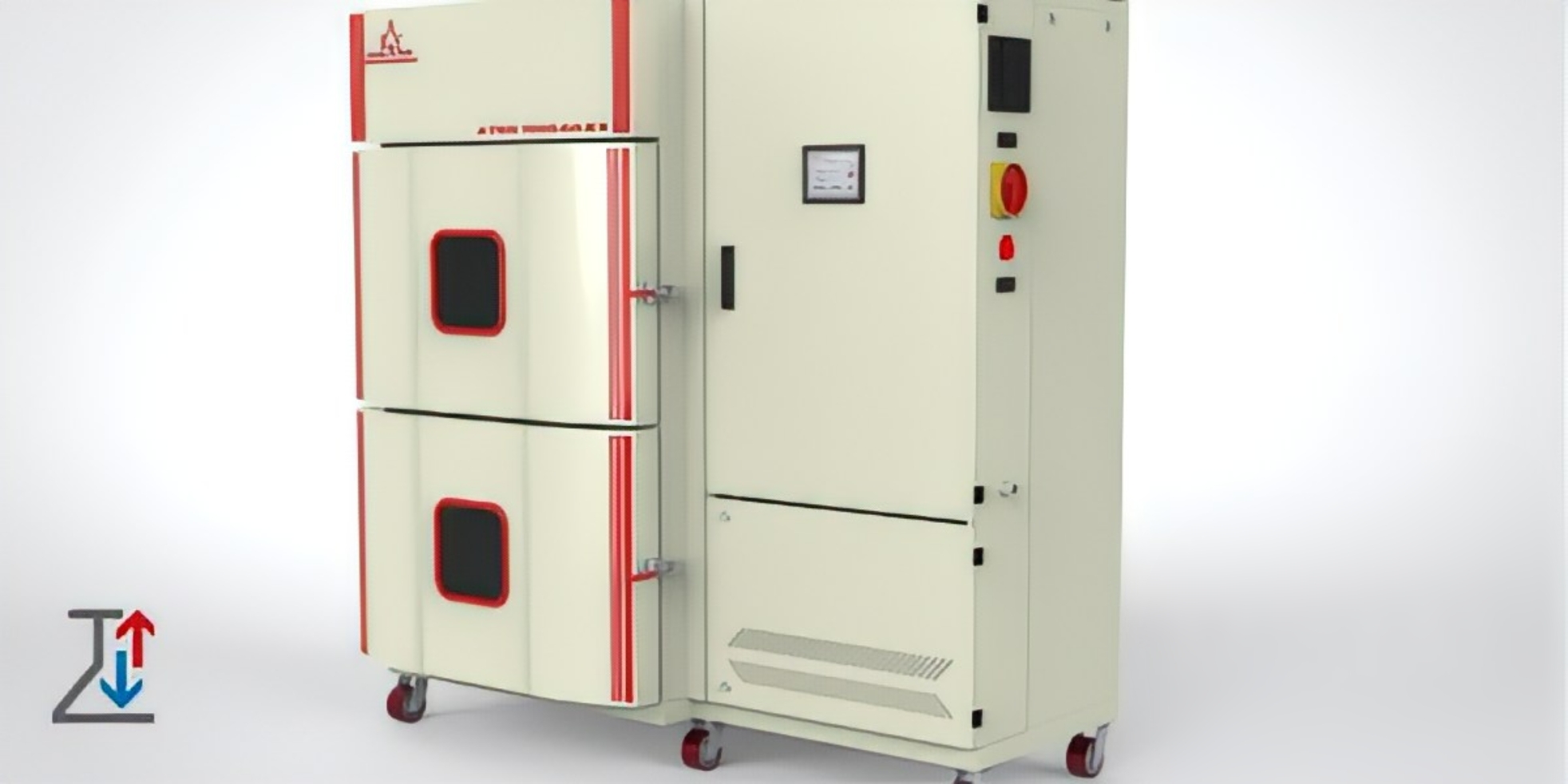
A thermal shock chamber is a specialized test device designed to simulate and evaluate the effects of sudden and extreme temperature changes on materials and products.
This controlled environment is critical for evaluating the durability, reliability, and performance of a variety of items, from electronic components to aerospace materials.
Click here for more information about the Solar Radiation Test Chamber.
What is a Thermal Shock Chamber?
A thermal shock chamber is a specialized testing device designed to subject materials and products to extreme and rapid changes in temperature. This type of testing helps to simulate real-world conditions where products may encounter sudden temperature fluctuations, allowing manufacturers to assess the durability, performance, and reliability of their materials or products when exposed to thermal stresses. thermal chambers are commonly used in industries like electronics, aerospace, automotive, materials science, and manufacturing to ensure that products can withstand harsh environmental conditions.
Key Features of a Thermal Shock Chamber
A thermal shock chamber is an environmental testing device used to simulate various temperature conditions to test the durability, performance, and stability of materials, products, or components. By subjecting items to controlled temperature fluctuations, thermal chambers allow engineers and researchers to predict how these products will behave in real-world environments. Here is a comprehensive list of features that you find in thermal shock chambers:
- Dual Temperature Zones
- Rapid Temperature Change
- Temperature Range
- Precise Temperature Control
- Programmable Testing
- Multiple Cycle Testing
- Fast Transfer Mechanism
- High-Performance Cooling System
- High-Performance Heating System
- Temperature Uniformity
- Automated Testing
- Data Logging and Reporting
- Touchscreen Interface
- Time Monitoring
- Overheat Protection
- Cold Zone Subcooling
- Safety Alarms
- High and Low-Temperature Alarms
- Energy Efficiency
- Programmable Hold Time
- Humidity Control
- Ethernet Connectivity
- Software Integration
- Test Sample Capacity
- Compact Design
- Large Chamber Options
- Corrosion Resistance
- Fast Recovery Time
- Customizable Temperature Rates
- Heat Insulation
- Low Noise Operation
- Increased Temperature Stability
- Test Chamber Observation Window
- Cooling Time Optimization
Hot Air Flow Circulation - Advanced Refrigeration System
- Cold Plate Technology
- Test Sample Holder
- Full Compliance with Standards
- Temperature Gradient Control
- Flexible Testing Configurations
- Test Item Protection
- Multiple Cycle Profiles
- Touchscreen Calibration
- Fast Temperature Recovery
- Overcurrent Protection
- Low-Temperature Saturation
- Energy Consumption Monitoring
- Automated Fault Detection
- Temperature Deviation Logging
- User-Defined Settings
- Compatibility with Environmental Chambers
- Continuous Test Monitoring
How a thermal shock chamber simulates extreme temperature changes
Thermal shock chambers are specifically designed to replicate rapid temperature transitions, ranging from freezing cold to intense heat. This simulation is crucial for testing materials that must endure extreme environmental conditions, such as electronics, automotive parts, and aerospace components.
The chamber achieves this by cycling through rapid temperature changes, typically in a matter of minutes. A product is placed inside the chamber, and the temperature is quickly dropped or increased to a set point. The chamber can also alternate between hot and cold extremes, making it possible to simulate the stresses experienced during thermal cycling in various environments.
Different Types of Thermal Shock Chambers
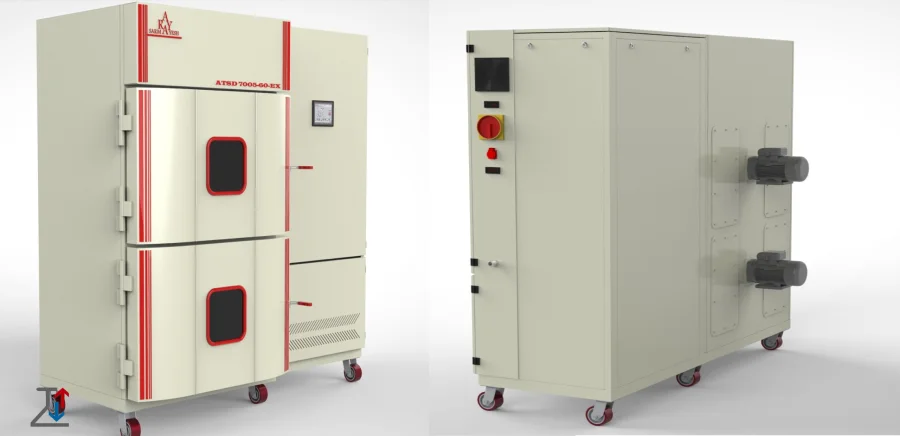
Thermal shock chambers come in several configurations, each designed to suit specific testing needs. The most common types are two-zone and three-zone thermal chambers. Understanding how each works can help you determine which type is best suited for your testing requirements.
1- Two-zone thermal chamber
A two-zone thermal shock chamber is the most basic and commonly used configuration. It consists of two separate zones: one for heating and one for cooling. The test sample is typically moved between these two zones, exposing it to both extreme hot and cold temperatures. This type of chamber is ideal for testing products that need to endure rapid thermal transitions between two distinct temperature extremes.
How It Works: In a two-zone system, the product is moved from one zone to the other. The heating zone uses elements like infrared lamps or resistive heaters to quickly raise the temperature, while the cooling zone employs refrigeration systems or cryogenic liquids (like liquid nitrogen) to rapidly cool the sample.
Use Cases: Two-zone chambers are suitable for products that need to be subjected to extreme heat and cold in a relatively short amount of time.
2- Three-Zone Thermal Shock Chamber
A three-zone thermal shock chamber adds an intermediate zone between the heating and cooling areas. This middle zone, often referred to as the “transition zone,” allows for a more gradual change in temperature. The primary advantage of this design is that it can reduce the stress caused by sudden temperature shifts, making it ideal for more delicate products or materials that require slower transitions to avoid immediate failure.
How It Works: The three-zone chamber is divided into three distinct temperature regions: a hot zone, a cold zone, and a transition zone.
The test specimen is typically transferred through all three zones, first entering the hot zone, then moving through the transition zone before reaching the cold zone, or vice versa. This gradual movement reduces the thermal shock on the sample.
Use Cases: Three-zone chambers are often used for high-precision applications, such as aerospace, medical device testing, or research into new materials that may be sensitive to extreme thermal changes. The transition zone allows for a more accurate simulation of real-world conditions, especially in industries where components experience gradual temperature shifts, such as in high-altitude environments or during transport.
3- Vertical vs. Horizontal Thermal Shock Chamber
While the two and three-zone configurations are the most critical distinction, thermal shock chambers can also be categorized by how they move the test sample.
Vertical Thermal Shock Chambers: In vertical models, the sample is lifted or dropped vertically from one zone to the other. This type is often used for testing smaller items or items that may not require a continuous transfer system.
Horizontal Thermal Shock Chambers: In horizontal models, the sample is moved from one zone to the other along a horizontal conveyor or rail system. This type is more suitable for larger or bulk items, or when faster sample transfer is required.
Which thermal shock chamber should be used for tests that move the test subject?
Our suggestion for tests where the movement of the tested material does not affect the test results is chambers equipped with a movable lifting cage. This will reduce early failures and increase the reliability of your products.
Specialized Thermal Chamber Design:
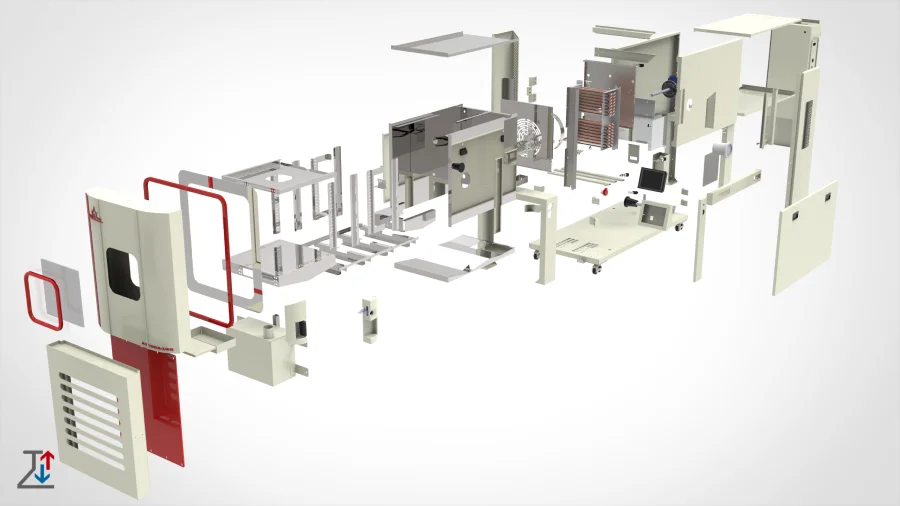
Thermal chambers can be tailored to a range of specifications, depending on the type of testing required and the products being tested. These chambers can vary in size, temperature range, heating and cooling speed, and control precision.
We recognize that different industries have unique testing requirements, which is why we offer customizable options for our thermal shock chambers. Whether you need specific temperature ranges, special chamber sizes, or integrated systems such as humidity control, we can design a solution that fits your needs.
If your testing involves sensitive electronics, for example, we can provide options that minimize vibration and prevent electromagnetic interference. For industries that require altitude simulations, we can integrate pressure control systems to mimic high-altitude conditions. Whatever your needs are, our team works with you to ensure that the thermal shock chamber is perfectly suited to your testing environment.
Purpose of Thermal Shock Chamber:
The main purpose of the thermal shock chamber is to expose the material or product to rapid and sudden temperature changes and to handle practical situations where objects may undergo sudden temperature changes, These tests are important to identify vulnerabilities, weaknesses, or potential defects in the materials that may occur during use.
By exposing samples to extreme conditions in a controlled environment, engineers and researchers can evaluate the effects of thermal shock and refine designs to improve performance and longevity.
Below is a list of key purposes for using a thermal shock chamber:
- Material Resilience
- Detect Structural Weaknesses
- Accelerated Aging Testing
- Assess Electronic Component Reliability
- Quality Control in Manufacturing
- Regulatory Compliance and Certification
- Optimize Product Design
- Test Adhesion of Coatings and Materials
- Prevent Product Failures in Extreme Environments
Operating Principles of Thermal Shock Chamber
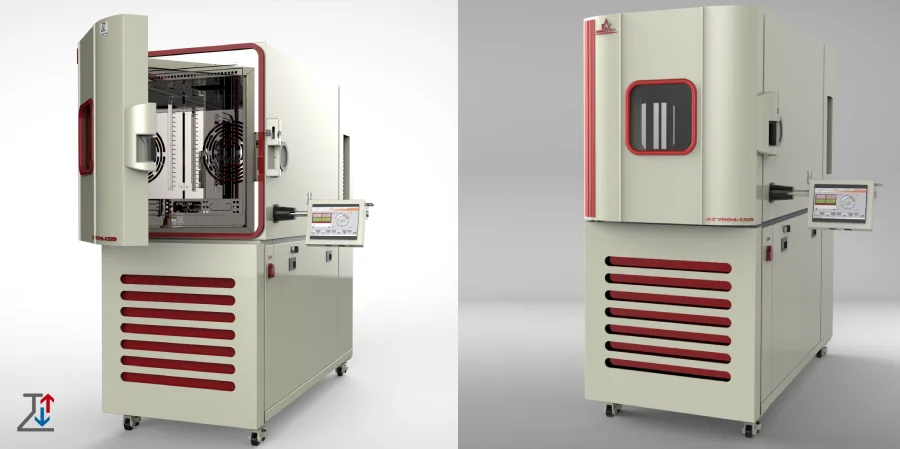
Thermal shock chambers operate through controlled temperature manipulation. The chambers are equipped with sophisticated heating and cooling systems that can rapidly change the environment inside the test chamber. The two primary methods for achieving extreme temperature variations are:
Two-Zone or Three-Zone Chambers: In a two-zone thermal chamber, there are separate hot and cold compartments, each with its own temperature control system. The test specimen is rapidly transferred between the two zones, exposing it to sudden temperature transitions. In a three-zone system, a middle zone acts as a buffer or transition area, allowing for smoother temperature changes.
Rapid Temperature Cycling: Thermal shock chambers employ precise control mechanisms to rapidly cool or heat the chamber, often using forced air circulation, liquid nitrogen, or specialized refrigerants to achieve the desired temperatures. The systems are designed to reach extreme temperatures quickly, within seconds or minutes, ensuring that the tested materials are subjected to stress similar to real-life thermal shocks.
Temperature Ramp Rates: These chambers are programmed to achieve a specific “ramp rate” or the speed at which the temperature increases or decreases. This rate is crucial to simulate real-life conditions, where sudden temperature fluctuations can cause materials to expand or contract at varying speeds, potentially leading to cracks or structural failures.
Benefits of using a thermal chamber:
The thermal chamber helps prevent costly recalls and warranty claims by fixing potential problems before the product hits the market. The ability to reproduce extreme temperature conditions in a controlled environment allows engineers and researchers to improve the reliability, durability, and performance of a wide range of materials and products.
A thermal shock chamber is a crucial tool in industries that require rigorous product testing. It rapidly exposes materials or components to extreme temperature fluctuations, ensuring they can withstand harsh environmental conditions. Here are the key benefits of using a thermal shock chamber:
- Enhances Product Reliability
- Accelerates Product Development
- Detects Material Defects Early
- Reduces Risk of Product Failures
- Improves Customer Satisfaction
- Supports Multiple Industries
- Saves Costs in the Long Run
Why Thermal Shock Testing is Critical for Product Durability
Thermal shock testing simulates the kind of temperature fluctuations that products might experience during their lifecycle. In many real-world applications, products are exposed to environments where they are rapidly heated or cooled, which can cause stress to the materials, leading to cracks, deformations, or even catastrophic failure. For instance, an electronic device may experience both extreme heat from internal components and sudden cold when exposed to outdoor conditions, or an automotive part might face extreme temperature changes during use in different climates.
Manufacturers can set and maintain high standards for product durability and performance by subjecting products to rigorous temperature cycling. Identifying and correcting design errors and material weaknesses early in the development process can lead to significant cost savings. Here are some benefits of using a thermal chamber:
- Enhanced Product Performance
- Improved Design
- Risk Mitigation
- Faster Time to Market
Application of thermal shock chamber
Thermal shock chambers are imperative devices used in different businesses to test the versatility and unwavering quality of items subjected to extraordinary temperature changes. These chambers mimic fast moves between hot and cold situations to survey how materials, components, or gadgets withstand such stresses. Here’s a closer look at their applications:
- Electronics (testing circuit boards, semiconductors)
- Automotive (evaluating engine components, plastics)
- Aerospace (ensuring material stability in extreme altitudes)
- Medical Devices (validating performance of implants and instruments)
- Consumer Products and Packaging
Why Is Thermal Shock Testing Important?
Thermal shock testing is crucial for ensuring that products can survive and perform under extreme and rapidly changing temperature conditions. Products exposed to these conditions can experience various damage, such as cracking, warping, loss of functionality, or even complete failure. Thermal shock testing helps identify these vulnerabilities early in the product development process.
Here are some key reasons why thermal shock testing is essential:
- Product Durability and Reliability
- Quality Control
- Compliance with Industry Standards
- Cost Savings
Thermal Shock Chamber price
Thermal shock testing is an essential part of the product development process, ensuring that materials can withstand rapid temperature fluctuations without failing. However, acquiring a thermal shock chamber can be a significant investment, especially for small to mid-sized companies or research organizations. That’s where we come in.
Our thermal shock chambers offer the same level of precision and reliability you would expect from high-end, expensive models without the steep price tag. We’ve combined cutting-edge technology with cost-effective manufacturing processes, allowing us to pass the savings directly on to our customers.
While many thermal chamber manufacturers focus on premium pricing, we prioritize making these essential testing tools affordable for a wider range of businesses. Our thermal shock chambers are built using high-quality components that meet international standards, ensuring accurate temperature control, reliable performance, and long-lasting durability. Despite offering a lower price point, we never compromise on the quality and features that are crucial for high-level testing.
For a free consultation with our experts, please contact us.
Purchase of thermal shock chambers:
Investing in one of our thermal shock chambers is a smart decision that will help you improve your product testing, ensure durability, and speed up your development process all while staying within your budget.
When you purchase a thermal chamber from us, you’re not just buying equipment—you’re gaining a long-term partner in your testing processes. Our team of engineers and technicians provides expert support from initial consultation through installation and ongoing maintenance. We ensure that you are fully trained to operate the chamber effectively, and we’re always available to provide troubleshooting assistance when needed.
Our customer service team is committed to making your experience seamless, from answering technical questions to ensuring that the shipping and installation process is as smooth as possible. With our knowledgeable and responsive team by your side, you can feel confident that your testing processes will be efficient and hassle-free.
We know that time is a critical factor when it comes to product development and testing. That’s why we offer fast turnaround times for both manufacturing and shipping. Once you place your order, our team works diligently to ensure that your thermal shock chamber is manufactured, tested, and shipped as quickly as possible. We also offer flexible delivery options to meet your timeline requirements.
Whether you need the chamber for urgent testing or have a planned installation schedule, we can work with you to ensure that your equipment arrives on time and ready to use.
Aryasarmayesh Company is proud to have provided the conditions to produce thermal shock chambers to test combustible and flammable chemical materials for your convenience, dear buyers.
Aryasarmayesh thermal shock chamber can be equipped with an external dry air production system, which can prevent the formation of dew on the test piece and will be optional.
Thermal chambers expose products to extreme temperature changes, shifting rapidly between hot and cold zones. They’re used to test materials and components for thermal stress tolerance, often in electronics, automotive, and aerospace industries where rapid temperature shifts are common.