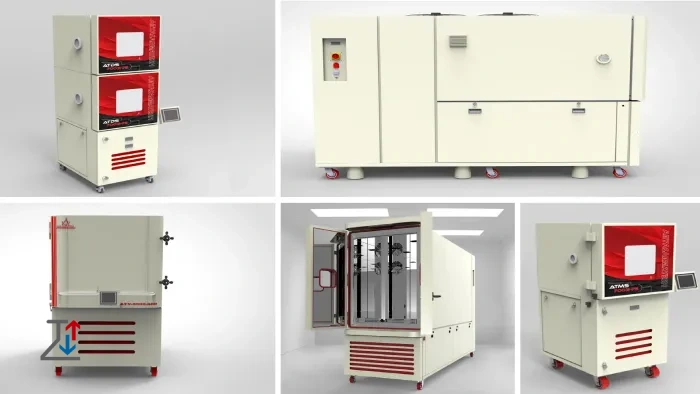
Electronic component test chambers are essential tools in evaluating the durability, reliability, and performance of electronic devices under various environmental conditions. These chambers simulate extreme temperatures, humidity, pressure, and other environmental factors that electronic components may face in real-world applications.
What is an Electronic Component Test Chamber?
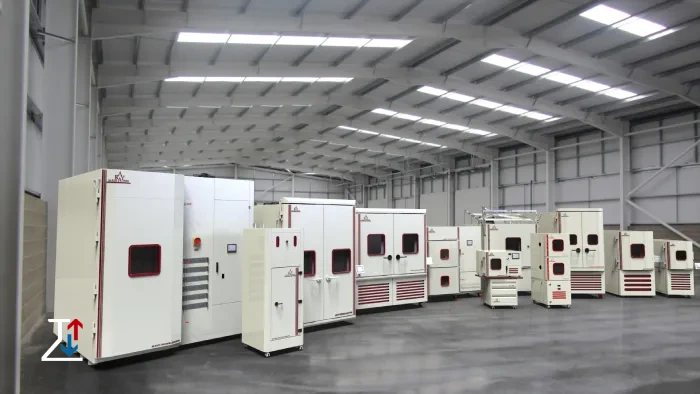
An electronic component test chamber (also known as an environmental test chamber) is a device used to simulate different environmental conditions such as temperature, humidity, and pressure in a controlled setting. These chambers are designed to test the endurance of electronic components under extreme conditions, ensuring that they function properly under real-world stress.
The primary function of these chambers is to replicate the environmental conditions that electronic components might experience in their operational life cycle. Test chambers provide controlled temperature and humidity variations and can simulate rapid temperature changes, high or low pressure, and other extreme environmental factors.
How Do Electronic Component Test Chambers Work?
Test chambers are equipped with several systems designed to control and monitor environmental conditions:
- Temperature Control: Test chambers are equipped with both heating and cooling systems to regulate temperature. The chambers can achieve a wide range of temperatures, from extreme cold (as low as -70°C) to extreme heat (up to 180°C or higher). These temperature fluctuations help simulate how electronic components will react to thermal stress.
- Humidity Control: These chambers can also regulate the level of humidity inside the test environment. This is critical for assessing the impact of moisture on electronic devices, especially in industries such as automotive or defense where components may be exposed to humid or wet conditions.
- Pressure Regulation: Some chambers offer the ability to simulate high or low atmospheric pressure. This is essential for testing components intended for use in high-altitude or space applications, where pressure conditions differ significantly from standard atmospheric pressure.
- Shock and Vibration Simulation: Advanced test chambers can simulate environmental shocks, such as thermal shock (rapid temperature changes) or mechanical vibration. These tests help determine how components will react to abrupt environmental shifts or mechanical stresses.
- Data Collection and Monitoring: Most test chambers come with integrated systems to continuously monitor and log data regarding the performance of the components under test. Sensors inside the chamber measure temperature, humidity, and pressure, and the data is recorded to evaluate any performance degradation or failure modes.
Types of Electronic Component Test Chambers:
- Thermal Chambers: These chambers are primarily used for testing electronic components under various temperature conditions. They can achieve high heat and freezing cold temperatures to simulate extreme environments.
- Thermal-Humidity Chambers: These chambers combine both temperature and humidity control, allowing for more complex testing scenarios. They are often used in industries like automotive or aerospace, where components may be exposed to both heat and moisture.
- Altitude Chambers: Designed to simulate high-altitude conditions, altitude chambers reduce the air pressure inside the chamber, allowing manufacturers to test how components perform under low-pressure environments.
- Vibration Test Chambers: These chambers combine environmental simulation with vibration testing to assess how components withstand mechanical stresses. These chambers are critical for testing components in transportation or aerospace, where vibration is a common factor.
Importance of Test Chambers in Various Industries:
The rapid advancement in electronic technology has led to an increasing demand for high-quality, reliable components across numerous industries. Whether for consumer electronics, automotive, aerospace, or defense, ensuring that these components perform under extreme conditions is critical. Electronic components must withstand a variety of environmental challenges, including extreme temperatures, fluctuating humidity, and pressure changes. Test chambers designed for this purpose provide a controlled environment to simulate these conditions and assess the performance and lifespan of components.
- Aerospace: Components used in aerospace applications must endure extreme temperature and pressure changes, along with radiation exposure and mechanical vibrations. Test chambers allow for precise testing of these components to ensure their functionality in space, during flight, or in other challenging environments.
- Automotive: Electronic components in vehicles are exposed to a wide range of temperatures and humidity levels, along with mechanical shocks from driving. Test chambers allow automotive manufacturers to ensure the reliability of their components under these conditions.
- Consumer Electronics: Test chambers help consumer electronics manufacturers ensure their products will withstand environmental conditions that users might encounter, such as high temperatures, moisture, or electrical storms.
- Defense: Military and defense applications require equipment to perform reliably in extreme conditions, including high altitudes, sub-zero temperatures, and varying humidity levels. Test chambers are vital in ensuring that these components meet the rigorous standards for deployment.
Benefits of Electronic Component Test Chambers:
- Enhanced Reliability: Test chambers help identify potential weaknesses in components before they are released to the market. By simulating extreme conditions, manufacturers can ensure that their products are robust and reliable.
- Quality Assurance: Regular testing in environmental chambers ensures that components meet the highest quality standards. This is crucial for industries where failure can have catastrophic consequences, such as aerospace and defense.
- Improved Product Longevity: By testing components under harsh conditions, manufacturers can predict their lifespan and optimize designs for durability, leading to longer-lasting products.
- Cost Savings: By identifying potential issues early in the manufacturing process, test chambers can save money by preventing the need for expensive recalls or repairs due to failed components in the field.
Conclusion:
Electronic component test chambers are indispensable tools for ensuring the quality, durability, and reliability of components used in demanding environments. Whether in aerospace, automotive, defense, or consumer electronics, these chambers provide critical insights into how electronic devices will perform under extreme conditions. Manufacturers rely on these test chambers to produce high-quality products that can withstand the stresses of real-world use, ensuring both customer satisfaction and safety.
Related articles in Aryasarmayesh: