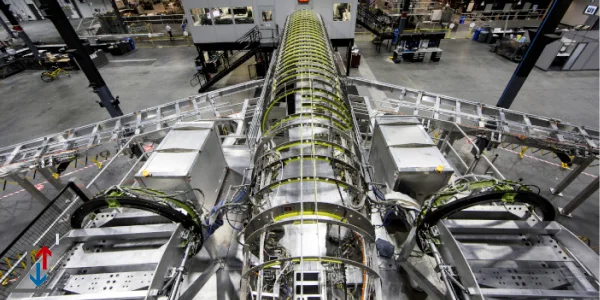
The testing process is considered a very important operation to achieve the desired outcome in producing and developing aerospace equipment. Mechanical tests of equipment and materials used in this industry are accomplished with high standards and the validation of aerospace industry materials and devices is considered a basic necessity. The Aerospace industry testing equipment is used for all these tests.
click here to read about the vibration-free chamber.
Aerospace industry equipment testing
Aviation test equipment will account for a significant share of the international Aerospace industry testing equipment market by 2028. The demand for aerospace test equipment is widely increasing in the aviation sector; they can analyze the behavior of different devices in real-time and measure the status by applying hydraulic, electronic, and atmospheric pressure tests. Some of these tests include mechanical resistance under high pressure, equipment performance, device behavior during increasing pressure, and resistance to hydraulic or electrical fatigue.
These tests give manufacturers an early idea of any technical or physical defects in current systems that finally, lead to increased safety. Because hydraulic and electronic test equipment is used to perform real-time tests, it provides manufacturers with a better view of the behavior of machines and materials used in the aerospace industry. In the following, we will mention four types of them.
Oxygen analyzer
This electrochemical analyzer is designed for accurate measurement of oxygen levels in most gases and industrial atmospheres. Oxygen analyzers use special types of electrochemical fuel cells and are very advanced instruments. They use simple software and the best type of sensors to provide accurate and reliable results under the most difficult environmental conditions.
Systech Illinois sensors are used to measure oxygen levels and can also be used for gas flows such as hydrogen, combustibles, hydrocarbons, and inert gases. These types of sensors are easily calibrated with ambient air in the testing of aerospace industries when traceable calibration gases can be used to meet very stringent quality assurance programs.
Thermal distortion meter
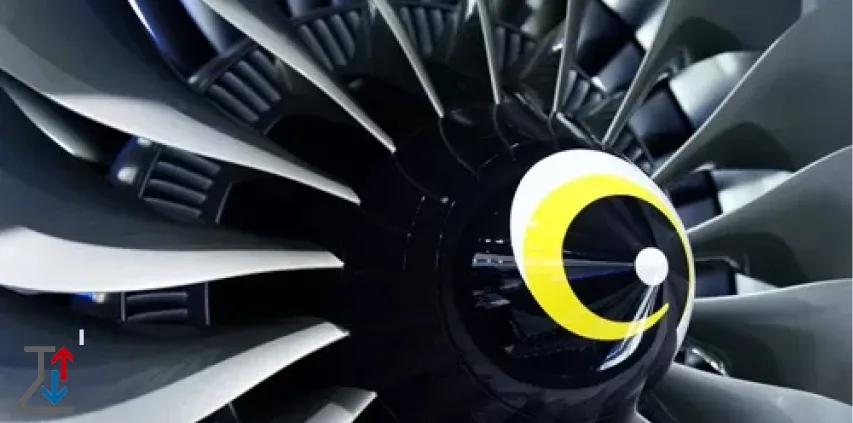
It performs multiple tests to cover international standards and uses microprocessor technology to accurately determine the distortion and softening point characteristics of all thermoplastic test samples. Two samples are tested simultaneously in the thermal distortion meter.
Simple and manual operation, as well as easy access to test sample response, are other features of this device. Each thermal distortion meter is equipped with a PT100 platinum resistance thermometer that accurately records the temperature of the side of the test sample to 0.1°C.
The built-in screen provides simple instructions on this type of aerospace test equipment and reduces user error. Thus, the test parameters are easily selected by the keyboard, a simple selection process is provided and the alarms make it very simple to perform the operational task.
The microprocessor temperature control function ensures that ramp rates of 50 or 120°C per hour remain within the desired test standard and also conducts non-standard ramp rates for customers’ specific needs. The test temperature of 300 0C can be easily achieved using this device and the nitrogen option is recommended to ensure optimal safety at higher temperatures.
Corrosion test chamber
C&W cyclic corrosion test chambers (CCT) are aerospace industry test equipment that are designed to accurately simulate the industry setting. Their reliability, ease of operation, and durable structure have led to the expansion of their use around the world and they are used in all major sectors such as automotive, paint, plastic, packaging, electronics, aerospace, military, and marine industries.
CCT is a durable, reliable, practical, and well-designed tool that is made of the best and highest quality materials and its overall structure is resistant to corrosion. It is made of glass-reinforced polyester (GRP) with a special formula, which shows high resistance to chemical corrosion and high temperatures.
This aerospace industry test tool has the option of wet or dry sealing and an ergonomic control panel. The Apex caps on this chamber are available in a wide range of composite materials for different testing needs and are supported by gas springs.
In general, it challenges the test sample under the worst state to ensure its quality under various conditions and exerts the strongest possible pressure on the test sample to avoid real-life problems and possible low-percentage damages.
CNC Laboratory
Another aerospace industry testing tool is vertical CNC. It is designed for rapid prototyping with three axes for cutting hard dense polymer sheets, laminates up to 40 mm thick, and polyethylene and polypropylene pipes used in the gas and water industry. Its compatibility with most materials used in the aerospace industry makes it a good choice for research and development departments, laboratories, and universities.
The CNC1 comes with Flashcut CNC software, a dedicated CNC software for use on a PC or laptop. This software has the highest programming standards and connects to the device with the least problems and the fastest time. CNC programs are pre-written directly by the device manufacturer and are available for any shape or size of the test sample or any international test standard.
Conclusion
Innovative test and measurement solutions can allow an engineer to identify and fix problems early in the development of a new technology. Often waiting until the end of a product’s life cycle can be costly, especially in the expensive aerospace industry.
Investing in aerospace industry testing can reduce the cost and more importantly the risk of projects. In fact, these conditions will help you to simulate the real space and by putting pressure on the parts, identify their defects and avoid the irreparable damages of testing in the real space.