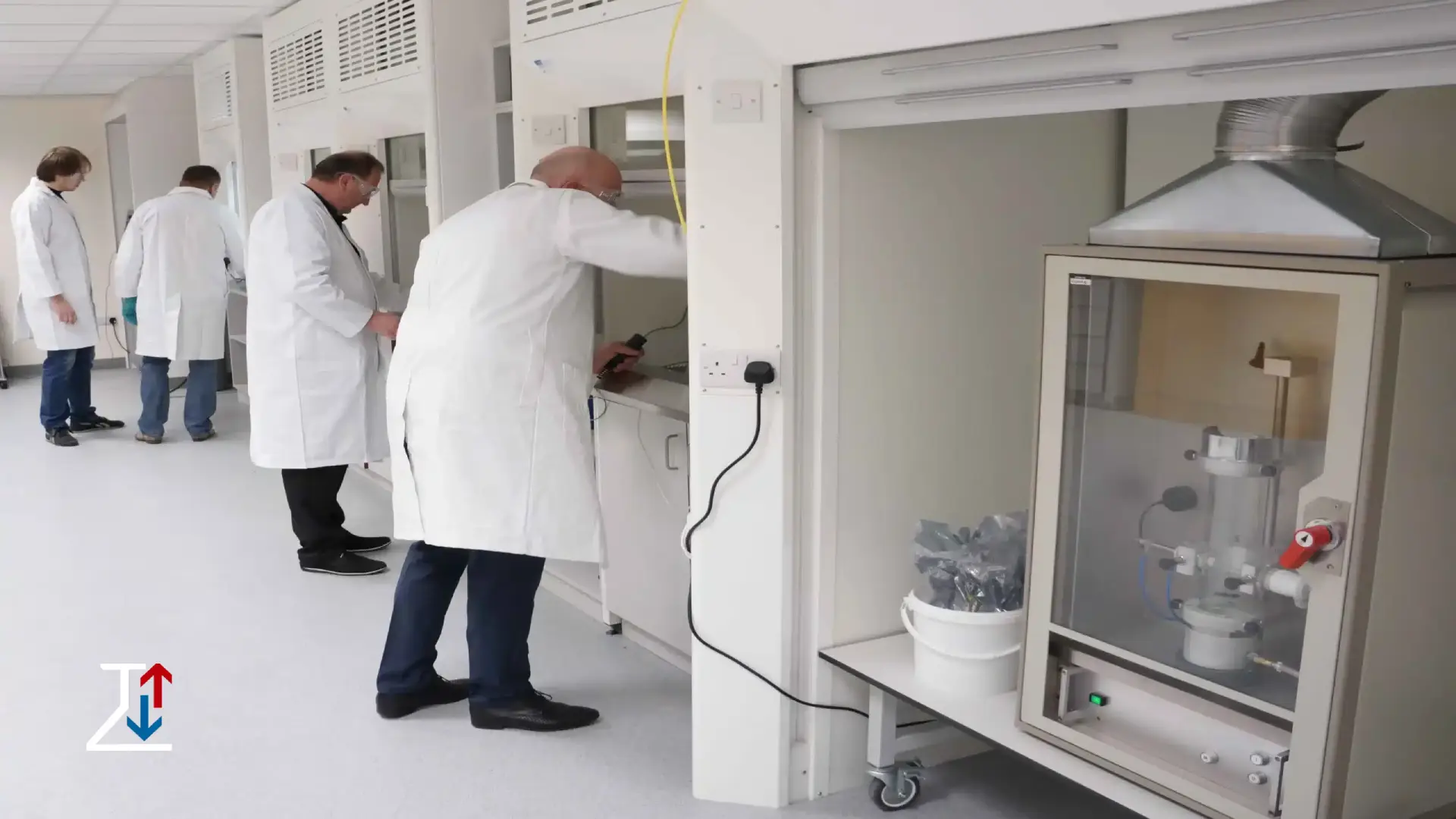
In an increasingly harsh and unpredictable environment, manufacturers need to ensure that their products can withstand various real-world conditions. One of the most common and potentially damaging environmental factors is dust. Dust exposure can affect products’ performance, longevity, and safety, particularly those used in electronics, automotive, aerospace, and military industries. Dust test chambers are utilized to simulate these conditions in a controlled setting.
What is a Dust Test Chamber?
A dust test chamber, also known as a dust chamber or dust resistance chamber, is a specialized testing device designed to simulate the effects of dust accumulation on products or materials. These chambers are engineered to recreate various environmental conditions that products might face, particularly in dusty environments. They subject the items to dust exposure for a set period, often under extreme temperatures, humidity, and mechanical vibrations, to assess their performance and durability.
The purpose of these chambers is not only to test for dust ingress (the ability of dust particles to penetrate the product) but also to evaluate the impact of dust accumulation on the functionality and integrity of the product over time.
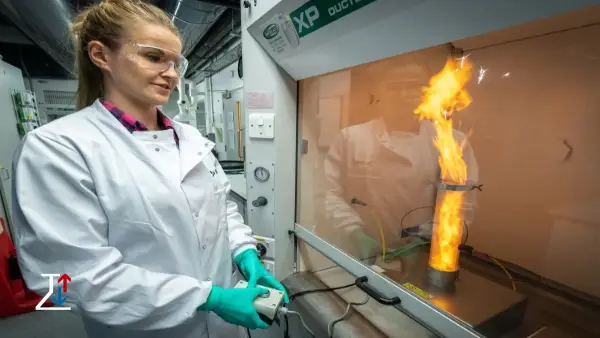
How Dust Test Chambers Work
Dust test chambers work by creating a controlled environment where dust particles are suspended in the air. Typically, the test chamber includes:
Dust Generation System:
A dust feeder or dust generator is used to release a consistent flow of dust into the chamber. Different types of dust can be used to simulate various environmental conditions, such as desert dust, industrial dust, or other particulate matter.
Chamber Environment:
The chamber maintains controlled settings such as temperature, humidity, and airflow. These factors are adjusted to simulate realistic operational conditions, like high temperatures or extreme humidity, in which dust exposure can be even more detrimental.
Test Samples:
The product or material being tested is placed inside the chamber. Depending on the product type and the industry standards, this could be an electronic component, a car part, an aerospace instrument, or a household appliance.
Test Duration and Intensity:
The testing duration and intensity vary depending on the product and its intended use. For instance, military equipment might undergo a longer, more intense dust exposure than a consumer electronic device.
Monitoring:
During testing, the chamber monitors several factors, including dust density, airflow, and the condition of the tested product. Instruments like cameras, thermometers, humidity sensors, and vibration monitors can help assess the impact of dust on the device or material.
Key Benefits of Dust Test Chambers
- Performance Validation: Dust chambers allow manufacturers to evaluate how well their products perform under dusty conditions. This helps ensure that the product will continue to function reliably in real-world dusty environments.
- Quality Control: These chambers help companies identify weaknesses or flaws in their products before they are released to the market. By detecting issues such as reduced electrical performance or component degradation due to dust, manufacturers can make necessary improvements.
- Enhanced Durability: Products tested in a dust chamber are more likely to be durable and resilient when exposed to dust in real-world conditions. This, in turn, improves customer satisfaction and reduces warranty claims.
- Risk Mitigation: By identifying potential dust-related issues early, manufacturers can prevent costly failures or recalls that might otherwise occur if the product were put to market without adequate testing.
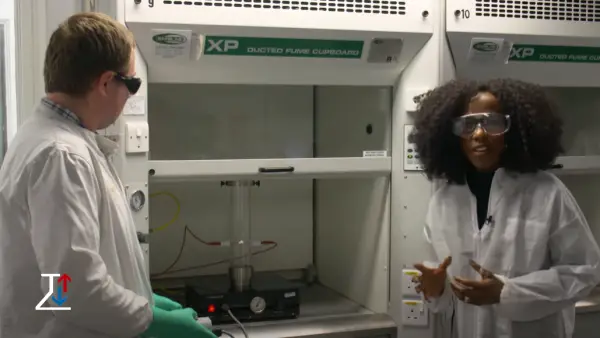
Applications of Dust Test Chambers
Dust test chambers are used across many industries to ensure product reliability in dusty environments:
Electronics and Appliances:
Electronics, such as smartphones, laptops, and televisions, often face dust exposure in households or outdoor environments. Appliances like refrigerators and air conditioners also need to be dust-resistant to ensure they continue to operate without failure.
Automotive Industry:
Cars, trucks, and other vehicles are exposed to dust on roads, particularly in desert regions or construction sites. Dust test chambers are used to ensure that vehicle components, such as engines, electronics, and air filters, function effectively in such environments.
Aerospace and Military:
Aircraft and military equipment are frequently subjected to dusty conditions in various operational zones. Dust test chambers are essential in ensuring that instruments, avionics, and engine parts can endure dust without compromising performance or safety.
Industrial Equipment:
Heavy machinery used in construction, mining, and agriculture often operates in dusty environments. Dust test chambers help ensure that the equipment’s vital systems, like hydraulics and electronics, can handle the harsh conditions.
Consumer Goods:
Products that are exposed to outdoor conditions, such as outdoor furniture, power tools, or sporting equipment, also undergo dust resistance testing to ensure their longevity and usability.
Conclusion
Dust test chambers play a critical role in assessing how well products can withstand the negative effects of dust exposure. They are an essential tool for ensuring that products are durable, reliable, and safe for use in environments where dust is a constant challenge. By simulating real-world dust conditions, manufacturers can identify potential failures, make necessary adjustments, and ensure that their products meet stringent industry standards. Whether in automotive, aerospace, electronics, or industrial sectors, dust test chambers help protect both the product and the end-user, guaranteeing a high level of performance and durability.
Read more: