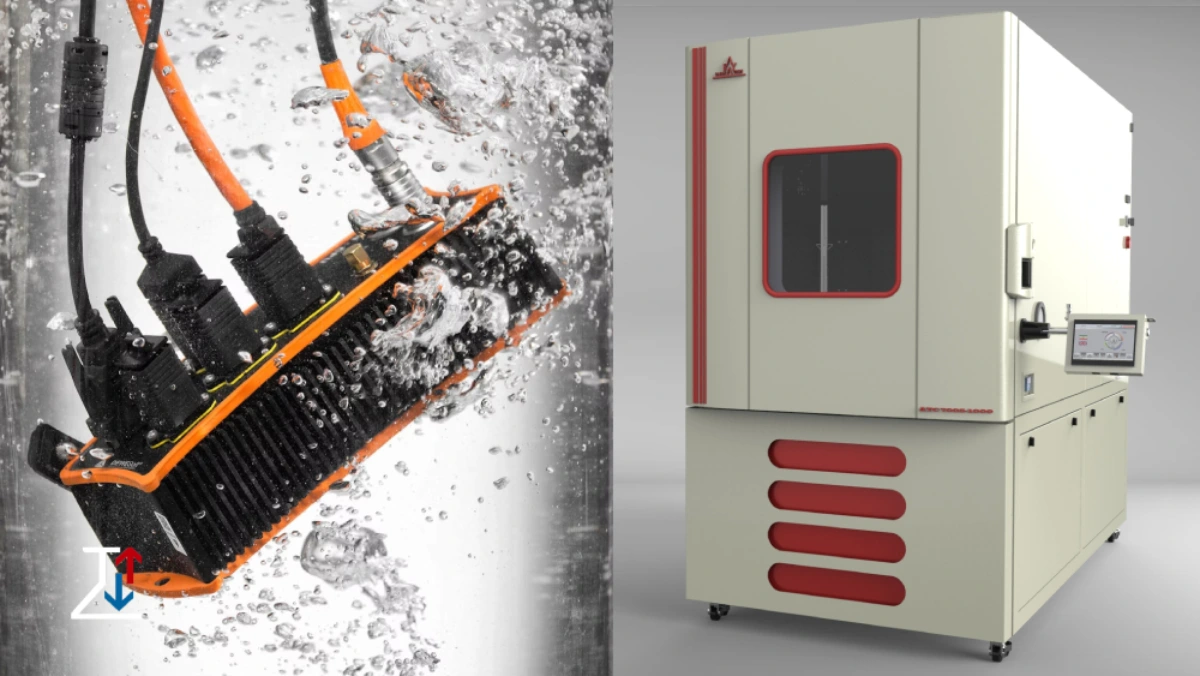
The durability and lifespan of industrial components are key factors in ensuring quality, safety, and optimal performance across various industries such as automotive, aerospace, electronics, oil and gas, and industrial equipment manufacturing. Durability testing is a vital process used to evaluate the resistance of components to various operational and environmental conditions. This article examines common durability testing methods and highlights the critical role test chambers play in the process.
Definition of Durability Testing
Durability testing refers to a set of tests designed to simulate real-world or extreme working conditions to assess a component’s resistance, longevity, and performance over a specified period. These tests are typically conducted during the product development or quality control stages, before the product reaches the market.
Common Durability Testing Methods
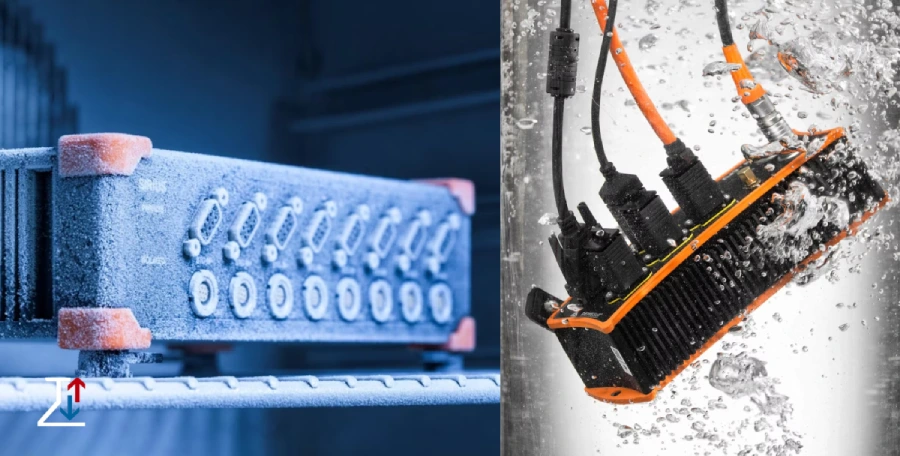
A) Mechanical Tests
- Fatigue Test: Involves applying repeated (dynamic) loads to a component to evaluate its resistance to failure or cracking over time.
- Wear Test: Assesses the surface resistance of a component to friction and material loss due to contact with other surfaces.
- Shock and Vibration Test: Examines the component’s ability to withstand sudden or continuous vibrations, especially relevant in transportation and defense industries.
B) Thermal Tests
- Thermal Cycling: Involves repeatedly heating and cooling a component to assess its resistance to expansion and contraction.
- Thermal Aging: Evaluates changes in a component’s properties over time under high temperatures, simulating material aging.
C) Environmental Tests
- Salt Spray (Corrosion) Test: Exposes the component to a saline environment to assess its resistance to rust.
- UV Testing: Subjects polymer and painted components to ultraviolet light to evaluate their resistance to sunlight.
- High Humidity and Temperature Test: Simulates hot and humid climatic conditions to assess material and component performance.
Challenges of Durability Testing in Real Environments
Conducting durability tests in real-world environments—such as operational fields or production lines—is often time-consuming, costly, and difficult to control. Therefore, tools are needed to simulate environmental and operational conditions accurately, consistently, and repeatably. This is where laboratory equipment like test chambers becomes essential.
What is a Test Chamber?
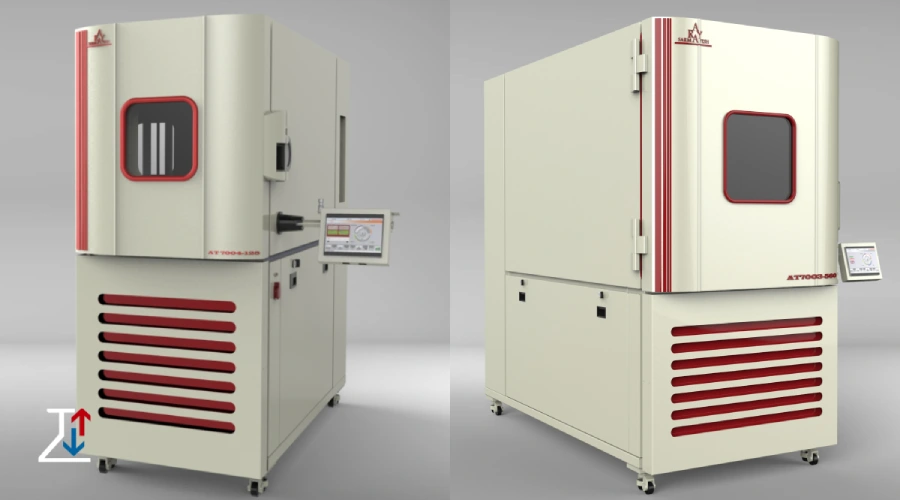
A test chamber, also known as an environmental test chamber, is a device that can precisely control and simulate various environmental conditions—such as temperature, humidity, pressure, UV radiation, corrosive gases, and thermal shock—within an enclosed space.
Types of Test Chambers and Their Applications
- Thermal Chamber: Precisely controls high or low temperatures to evaluate thermal performance.
- Humidity Chamber: Simulates high-humidity environments for aging or corrosion testing.
- Thermal Shock Chamber: Rapidly switches between extreme high and low temperatures to simulate sudden environmental changes.
- UV and Weathering Chamber: Tests components under sunlight and harsh weather conditions.
- Corrosion Chamber: Evaluates the resistance of metallic or coated components to rust.
Advantages of Using Test Chambers
- High precision in controlling test conditions
- Repeatability of experiments
- Reduced testing time via accelerated aging simulations
- Cost savings compared to field tests
The Role of Test Chambers in Assessing the Durability of Industrial Components
Test chambers play a crucial role in assessing the durability of industrial components. These devices simulate various environmental conditions to examine the performance and resistance of components or materials under harsh conditions.
Key Roles of Test Chambers in Durability Assessment:
- Simulating Real Environmental Conditions: Test chambers can simulate temperature, humidity, pressure, UV light, thermal shock, and more with precision. This helps manufacturers determine the conditions under which components may wear out, crack, or degrade.
- Accelerating the Aging Process: In many cases, waiting several years to evaluate a component’s long-term durability isn’t feasible. Test chambers accelerate the aging process using high temperature or humidity, allowing long-term effects to be assessed in a shorter period.
- Quality and Safety Testing: Tests such as thermal shock or rapid temperature changes help determine whether a component can remain stable under sudden environmental changes—critical to ensuring product safety and quality.
- Compliance with Standards: Many industries (automotive, aerospace, electronics, medical, etc.) must comply with international standards like ISO, ASTM, and MIL-STD. Test chambers enable testing in accordance with these standards.
Aryasarmayesh: Manufacturer of Environmental Test Chambers
In today’s competitive world, the durability and quality of industrial products are no longer optional—they are essential. Arya Sarmayesh, a leader in the design and manufacture of environmental test chambers, offers precise, reliable, and professional solutions to evaluate component performance under extreme conditions.
From simulating the scorching heat of deserts to the cold of the Arctic, from the intense humidity of tropical regions to the corrosion caused by sea salt mist, Arya Sarmayesh products ensure your components remain durable in any condition.
With Aryasarmayesh, durability is guaranteed before production begins.
Contact our experts today for a free consultation and choose the right product for your needs.
Conclusion
In the design and production of industrial components, durability testing plays a key role in ensuring product quality and performance. Various methods exist for conducting these tests, each simulating specific environmental conditions. However, to achieve accurate, repeatable, and reliable results, the use of test chambers has become essential. These devices recreate harsh environmental conditions in a lab setting, helping industries deliver higher-quality products to the market.
Related articles in Aryasarmayesh: